Anyone that has disassembled and/or built a four-cylinder Lycoming is probably very familiar with a specific nut – the one hiding underneath the cam gear. This little nut is the source of a great deal of mischief, for many forget to take it out (many because they don’t notice it) and then they wonder why the case halves wont come apart. Its also mischievous because it is darn hard to get out! This cleverly designed piece of frustration is situated in a way that almost no wrench ever made will fit. Either you can’t get to it because the gear is in the way (the gear is part of the cam shaft – forget about taking it off), or parts of the case casting are in the way. It is, pardon the pun, a tough nut to crack!
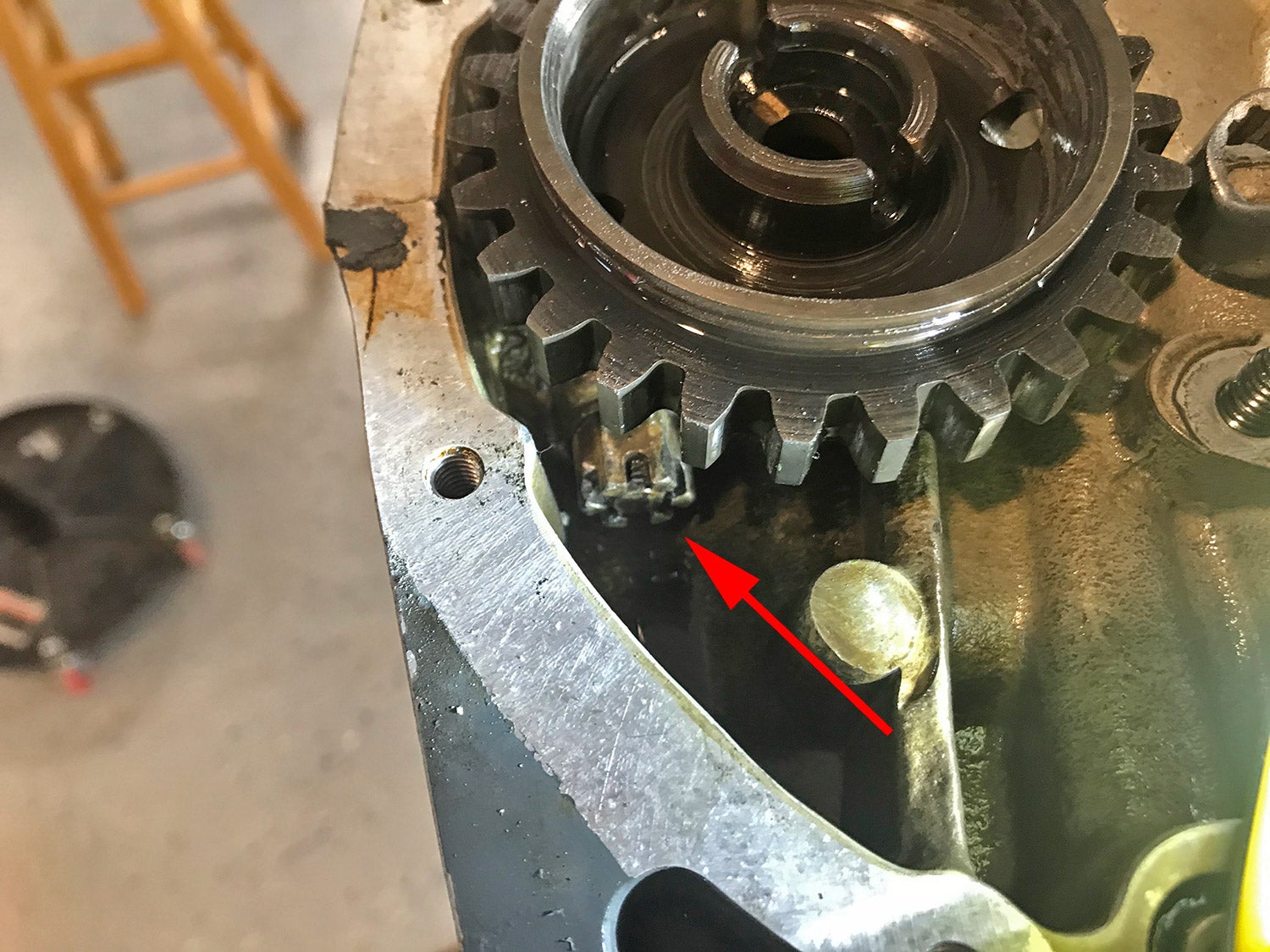
Now I have experience with these little things – I have built a few engines in recent years – but every time, it is a trial and error thing to figure out how to tighten it when assembling a motor. And if you’re disassembling, as I was with this motor today, well – who knows what gorilla tightened it when it was last touched? In our case, I am assuming that way back in 1992, Lycoming hired the Williamsport High School arm wrestling champion, a young man of great strength, and put him to work on the assembly line – because this thing just didn’t want to come off. I learned about this nut at Lycoming school, but that was a while back now, and when I went to my voluminous set of pictures from the classes, I found that the two that showed how we undid this fastener were blocked by our hands. More than 750 pictures and nothing to show for it.
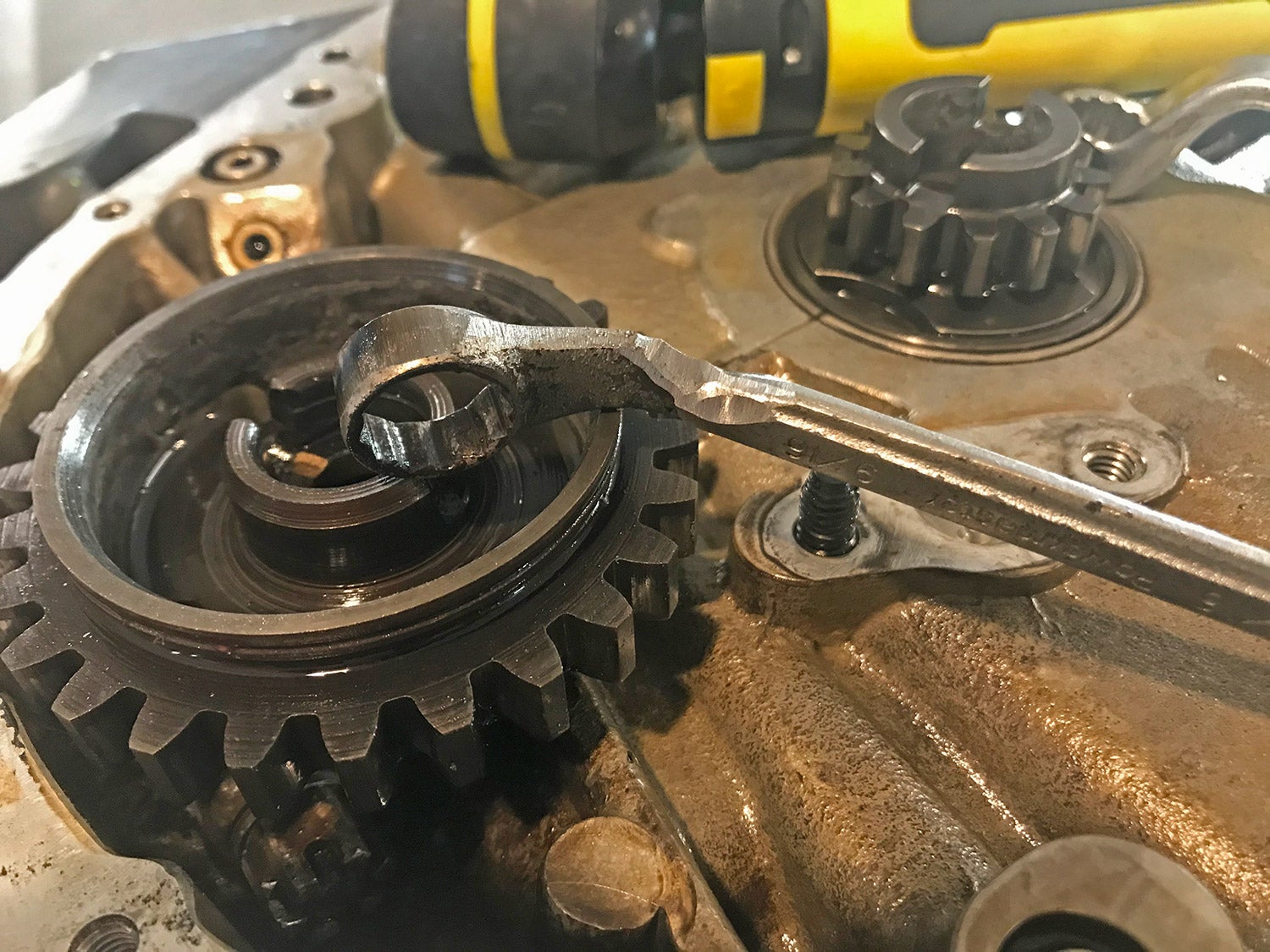
Of course, no socket will fit in there—that is right out. So we looked for an open end wrench – nope, too much of an angle to get a bite. We gave the castellated nut a couple of good whacks with a drift pin in one of the slots – but it just laughed at us. Next, out came the sacrificial wrench set—hmm, that 9/16” combination wrench looks like a good subject for torture and the set was only $10, so let’s fire up the power tools! I ground that box end until I could almost see through it, and sure enough, it cleared the case but at such an angle it just wouldn’t grab. OK—we need a bend here—big vise, heat, and hammer… well, it didn’t bend quite as close to the head as I wanted, but it goes on, and nope, it won’t turn—it was hitting the case again! More grinding until the handle is probably too weak to pull on – and nope – its a loose enough fit that it still hits the case when the slack is taken up.
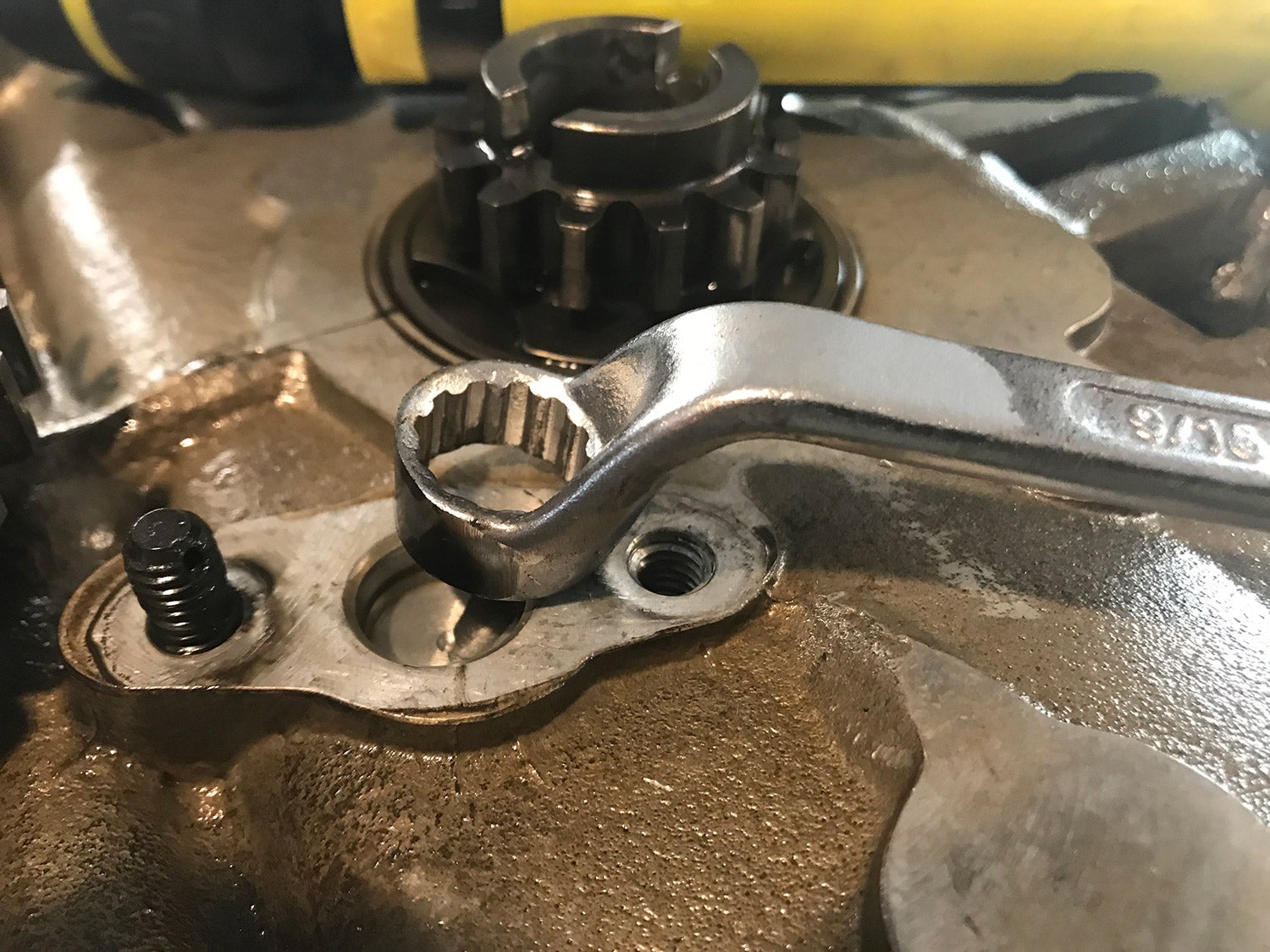
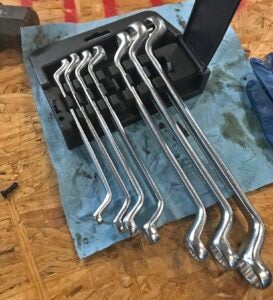
OK, its 5:00 pm, and Harbor Freight is a twenty five minute drive and closes at six! Off we go, and sure enough, they have a set of offset wrenches on sale—perfect as more torture victims. It’s always a shame when I have to buy a set to get one wrench, but this is aviation, and sacrifices have to be made. Home again, I saw that the shape was very promising – but why do they have to put so much metal on these things? Back to the bench grinder to produce a custom wrench that fits exactly in the spot – and allows a generous twelfth of a turn. With a satisfying pop I break the (undoubtedly now retired) young wrestler’s torque, and the rest was history. And the custom wrench goes into a special drawer for when it is needed again.
Kitplanes has the best articles. Thanks Paul for continuing to contribute to the knowledge base in such an entertaining manner.
A cylinder base wrench works perfectly!
Okay, Thanks Paul! I finally get to see a picture of this nut I have heard about.
Now how do you reinstall it properly?
Oh poor Paul. The experienced hands no that a cylinder base wrench does the trick and if your pulling a Lycoming apart you already have one on hand ! No Harbor Freight trips necessary.