Concretely explaining why a specific airplane appeals to a pilot is almost as easy as explaining why they fly. All Bob Bounds really knew when he first saw Fred Keller’s Prospector STOL, named Plansbuilt Grand Champion at EAA Oshkosh 1989, is that he wanted one. “I asked him if there were plans, and Keller’s answer was a strong and unequivocal ‘No!’,” said Bounds.
Bounds lives in Grant, Nebraska, a small town of 1200 people 20 miles south of the Ogallala exit on Interstate 80 and 18 miles east of the Colorado border. It is the seat of Perkins County, and he is its now-retired postmaster. “I now work in an auto parts store because my wife, Deb, says I have to; if I’m not working, I start building stuff.”
Stuff like a Rutan Quickie and VariEze. From the Grant Municipal Airport (GGF), Bounds flew the VariEze almost everywhere, including Keller’s home state, Alaska. “A cross-country airplane with teeny tires, there are not a lot of places you can fly a VariEze, so I wanted a different airplane,” and the Prospector remained at the top of his list.
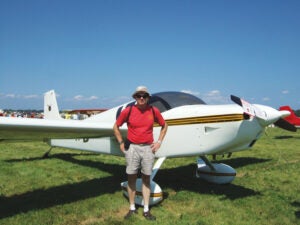
When a flying friend said he’d ridden in a Prospector, Bounds asked if he knew Keller. “No, it was a guy named Tom Couples. Maybe he’d have plans for it, so I called him up.” Couples and Keller were friends, so Keller built a Prospector for him. There were no plans, and that wasn’t the only bad news. Couples’ Prospector was a wreck; it choked on carb ice and went into the trees in Idaho.
With Bounds’ building experience, he said Couples told him, “You should be able to build one with what’s here.” Bounds had never heard of a homebuilder who’d used wreckage as 3D plans, so he wasn’t so sure about that. “Still, it wouldn’t hurt to look at it, so I loaded up my son and we drove to Kalispell, Montana,” Bounds said.
“I ended up buying it from him, thinking maybe I can do this.” Buying the remains in 2006 led, in part, to the airplane’s moniker, Checkered Past, said Bounds. “It was borne of a wreck and rebuilt from one.”
When they returned home with the trailer piled high with shrink-wrapped wreckage, Bounds said, “My wife was not very happy with me. ‘You were just going to look!’ Yeah, but look at this, I can make one of these! ‘Yeah, right,’ she said. And then it sat in my hangar for two or three months before I got enough nerve to go work on it.”
Burn Before Building
Bounds started work with a tape measure, legal pad and Sawzall. Initially, he’d planned to turn his measurements into plans, “but I was spending more time at the drawing board than in the shop.” Since he started with the wings, he has some pretty good drawings for them. The fuselage drawings are “mediocre, and the tail surfaces nothing, [but] I still have the templates for cutting the foam.”
To figure out the composite layup schedule and orientation he cut fiberglass coupons with the Sawzall and then set fire to them. “This burns all the resin out of them so you can see the layup schedule and orientation.” Labeling each structural biopsy—“this is the spar cap”—he’d peel them apart and make more notes.
Making its first flight in 2013, Bearcoupe construction “took seven years,” Bounds said. “Life gets in the way, but I just kept chipping away at it and worked on it pretty steady.” When he had to crawl over the structure that filled his two-car garage on the diagonal, he built a bigger shop in the backyard “and my wife could have her garage back.”

The Bearcoupe, and the Prospectors that preceded it, were built using Rutan-method moldless composite construction. “I didn’t vacuum bag anything.” Like Bounds, Keller had built a VariEze, which earned a grand champion award at Oshkosh in 1980. Burt Rutan presented the award, and that meeting led to a Defiant opportunity.
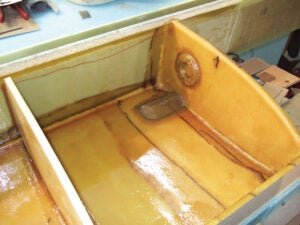
Rutan designed the four-place push-pull twin for certification and OEM production. When that didn’t happen, in 1981 Rutan asked Keller to build a Defiant from the OEM shop drawings and draft plans for amateur builders. Keller flew the result to Oshkosh in 1983. Fresh from that build, Keller designed the Prospector.
“The greatest challenge in reverse engineering the Prospector wreck was figuring out the sequence of building,” said Bounds. “So I built the wings first. After I got them done, I hauled in the pieces of the fuselage and started on that.”
He copied the Prospector’s wing system (designed specifically for Keller by the renowned John Roncz), which includes slotted flaps and drooping ailerons and the Keller STOL-1 airfoil. The October 1989 EAA Sport Aviation article said the system was mechanically simple and uncomplicated, but Bounds replaced its cables with pushrods because “Couples said there was a lot of slop in it.”
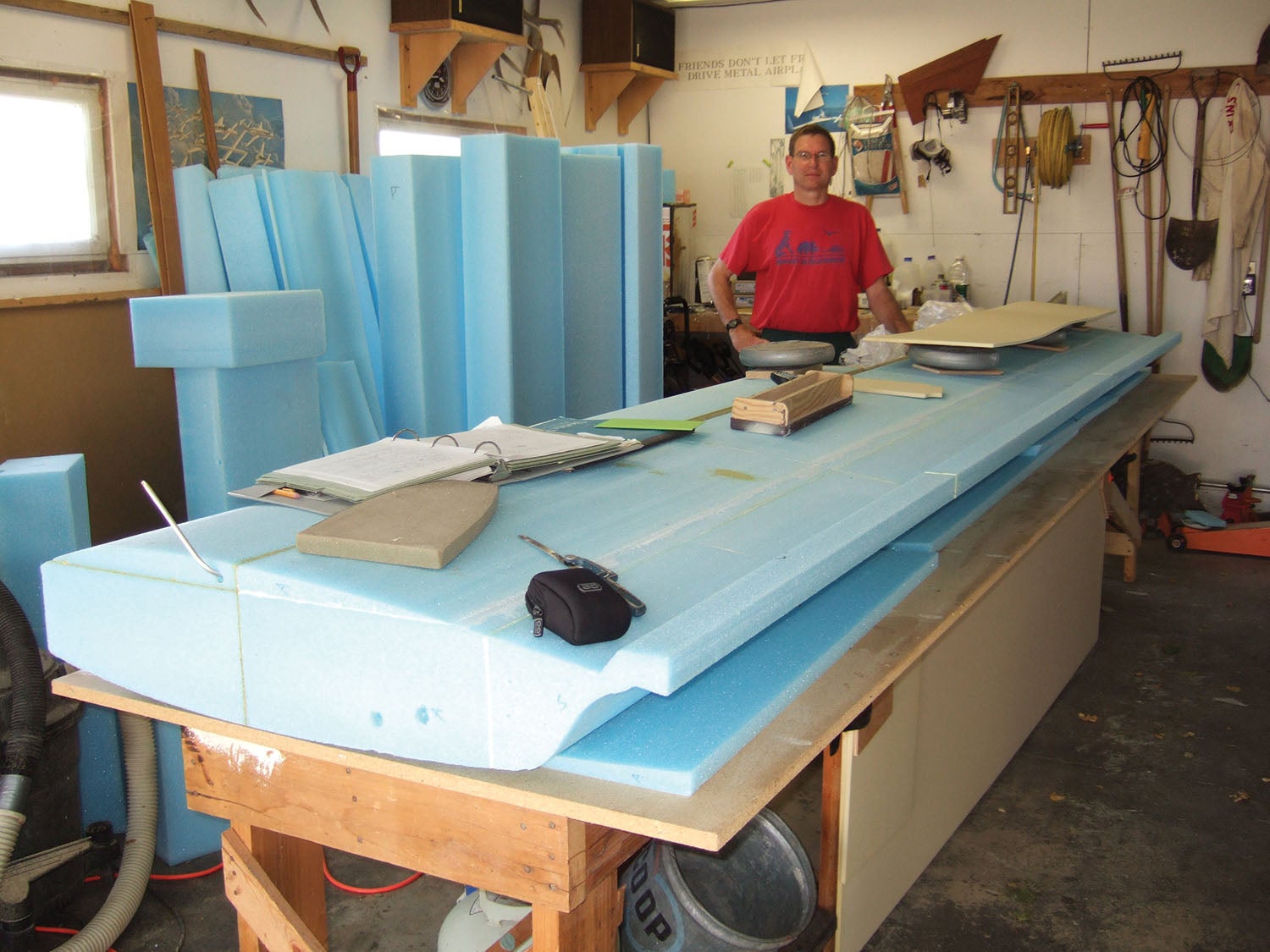
With a 34-foot span, the spar in each wing extends more than 3 feet past the root. These spars overlap each other and fit into a structural box behind the seat. “The wings actually sweep forward about 9 inches at the tip, so the spar can go behind your back,” he said. “You won’t notice it unless you see it from above or below.”
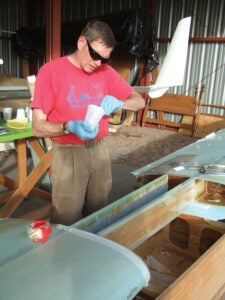
Like the Defiant, the wings have “pultruded” spar caps, Bounds said. It’s like an I-beam; builders dig out a trough in the foam core between the two fiberglass spar webs and fill it with S-glass twine pulled four strands at a time. “It takes 6 or 7 hours to fill the trough and then sand it level [once it cures].”
Describing the tool that wets the strands with epoxy, Bounds said he found one through the online Defiant groups. “A guy sent me his and told me to pass it along to the next builder in need because I don’t need it anymore.”
The flaps are huge, with extra layers of glass on the bottom to protect them from rocks thrown up by the tires and prop blast. Each one measures 8 feet by 14 inches. The ailerons are 6 feet long and droop at a 25% ratio, Bounds said. There are four notches of flaps to 40°, the setting where the ailerons droop 10°.
In converting the controls from cables to pushrods, Bounds decided on a center control stick with rudder pedals and brakes for both seats. He spent a lot of time “sitting at my kitchen table with my old trig book trying to figure out the layout and make it do what I wanted it to do.”
The Bearcoupe’s fuselage is slightly longer and wider than the Prospector, and the tail is different. “You can make the tail any shape you want,” Bounds said. He purposely replaced the original’s Cessna 180/185 angular outline with the sinuous profile of a WWII bomber, minus the tail gunner’s position.
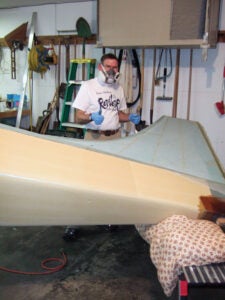
It’s a tribute to the late Ed Martins, friend, homebuilder and aviation mentor. “He was a farm boy who loved flying. A B-17 pilot, he flew 30 missions over Germany and had two DFCs [Distinguished Flying Cross, which recognizes heroism or extraordinary achievement while participating in an aerial flight]. He had some great stories.”
Worried about that B-17 tail, Bounds said the CG computations surprised him: “The CG is fine.” The inspecting DAR made sure of that. Beyond Bounds’s final numbers, “he wanted to see my scratch paper.” Fortunately, Bounds had saved all of it.
Apparently, a homebuilt the DAR had inspected crashed because the builder computed the CG using the spinner as the datum, said Bounds. He mistakenly used the main gear number as the datum when he computed the tailwheel figure, which made the airplane dangerously tail heavy. “The DAR was a sharp guy, and by checking my work he was going to make sure that I hadn’t made a similar mistake.”
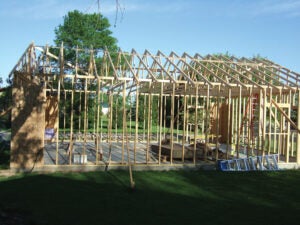
Keller designed the Prospector for backcountry operations, including hauling 12-foot boards to his lake cabin outside of Anchorage. They slid into the massive baggage compartment through the cockpit, and Keller designed the CG to accommodate them. It normally wears 8.50 tires, but it can also put on big bush wheels or skis. “The wheel pants are just for running around, like going to Oshkosh,” Bounds said. “Nobody makes them, so I had to. I’ve had a number of guys come up and ask ‘where did you get those?’”
While sketching a ream of unsatisfactory paint schemes, Bounds saw an ad for the Cessna TTX. “Its paint scheme was better than anything I could do, so I stole it.” Before applying the single-stage urethane, he did a lot of sanding. “As homebuilts go, the Bearcoupe is not a small airplane. You fill it, then block it all out, and do it all by hand with long, level sanding blocks to avoid ripples. It’s working on your upper body strength.”
A Dynon SkyView system with GPS, ADS-B Out and In, and transponder dominates the panel. “All that equipment is remotely mounted behind the rear bulkhead, which makes it handy to work on.” A panel-mounted MGL unit handles all the communication and intercom duties. “I installed all of the avionics, and wonder of wonders, it all worked!” said Bounds.
“I have an ancient O-340 in it. Rare birds, Lycoming only made them for about two years,” Bounds said. “I think they were made for the twin Navion because it needed more power than the 320 produced, so Lycoming stroked it. Two years after that, they came out with the O-360, and they quit building the 340.”
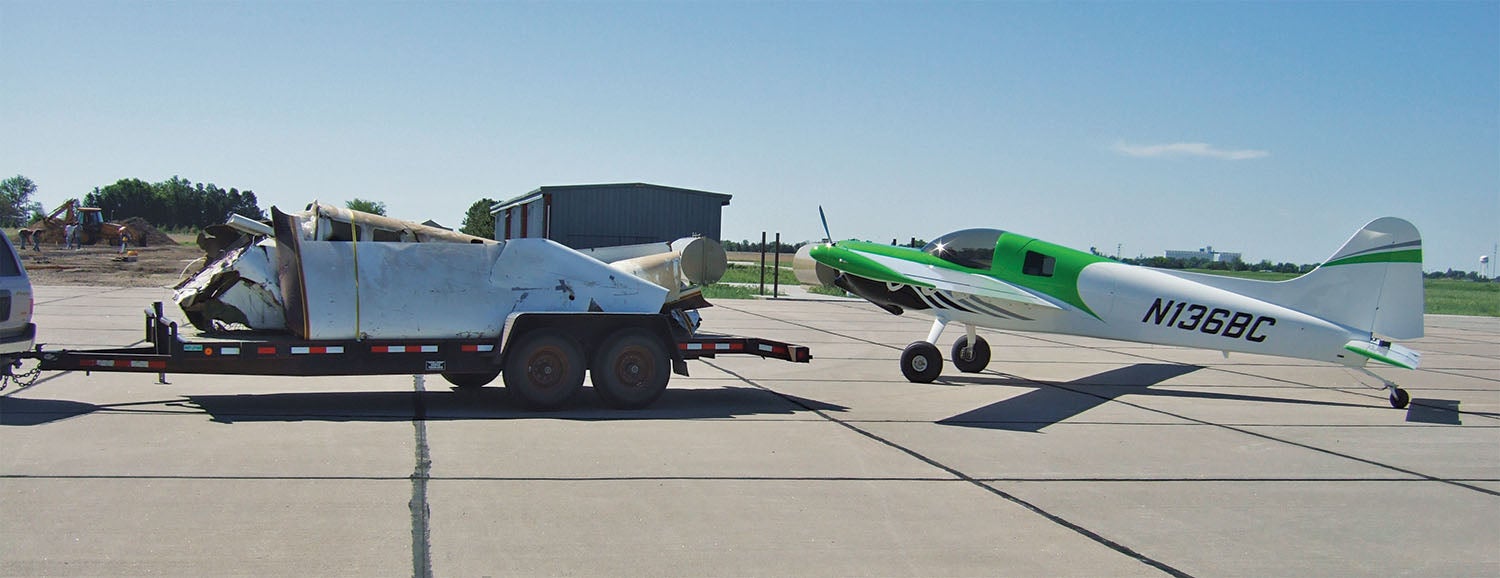
Bounds bought the four-cylinder, 170-horsepower Lycoming used. “It seems to pull the airplane well; I cruise at 115 knots and land at about 40.” It burns 13 gph wide open in a climb, but lean of peak at 11,000 feet it burns 5.5 gph at cruise. “With 55 gallons of fuel, it gives you enough to go out a bit farther—and get back—without crowding” the reserve.
Originally, the Lycoming turned a metal Sensenich propeller. Then he tried a Catto composite prop and became a fan. “I lost no takeoff performance and gained 10 mph, and it only weighs 13 pounds,” he said.
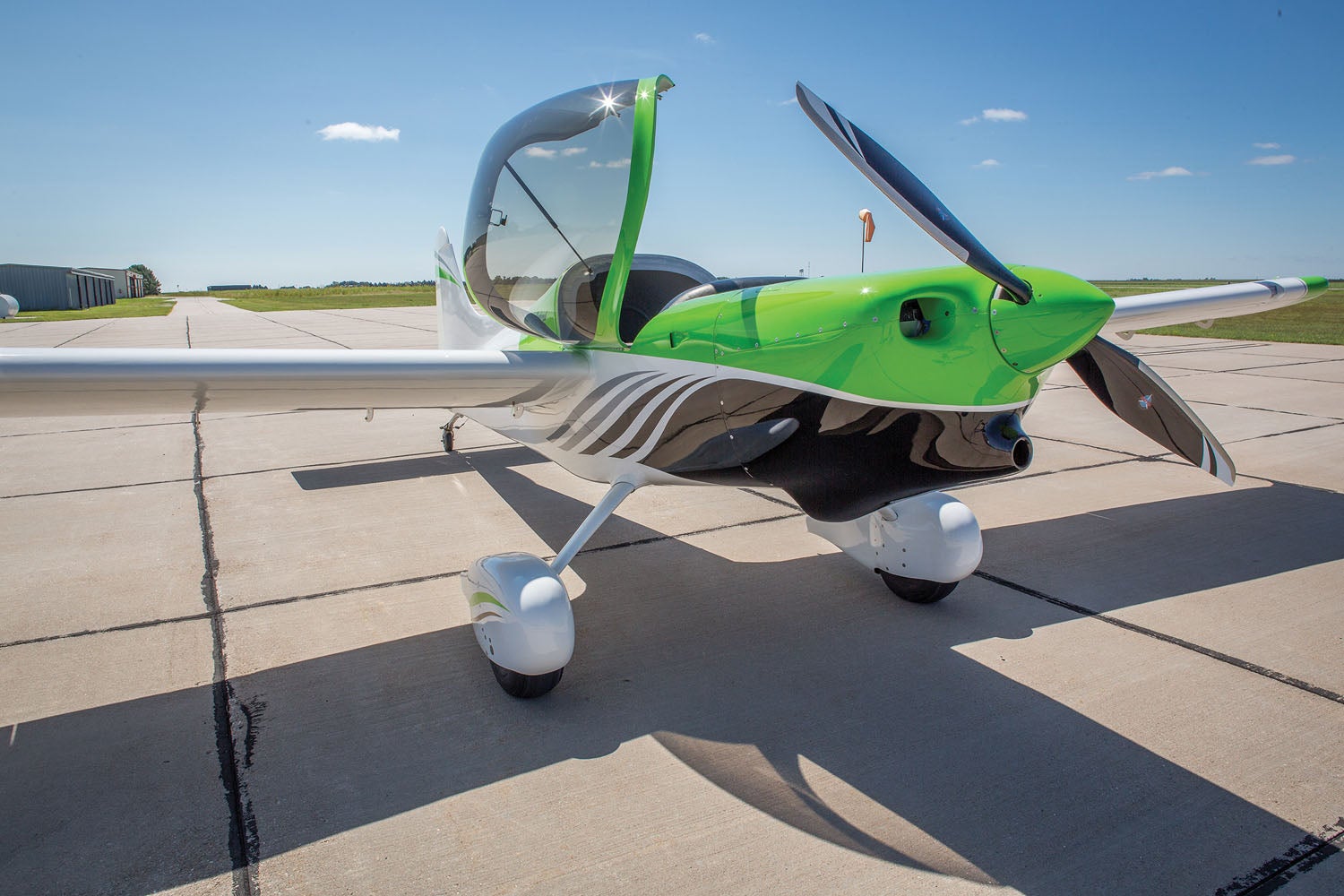
First Flight
The first flight in June 2013 went well, said Bounds. Like many newborn homebuilts, it had some teething problems. The anti-servo tab ratio on its all-flying stabilator was wrong. “If you let go [of the stick] it would diverge, then start getting worse and worse.” After making incremental adjustments, “it’s stable now, and you can upset it now and it will resume level flight,” Bounds said.
“It is the gentlest taildragger I’ve ever flown. I taxi at 20 knots, looking around, and it just rolls so straight. And it lands slow. I learned from the backcountry guys that the secret to getting into those strips is to get slow early and drag it in a bit. If you come in too fast, you can’t get rid of the extra speed, and some of those strips are one-way in and one-way out.”
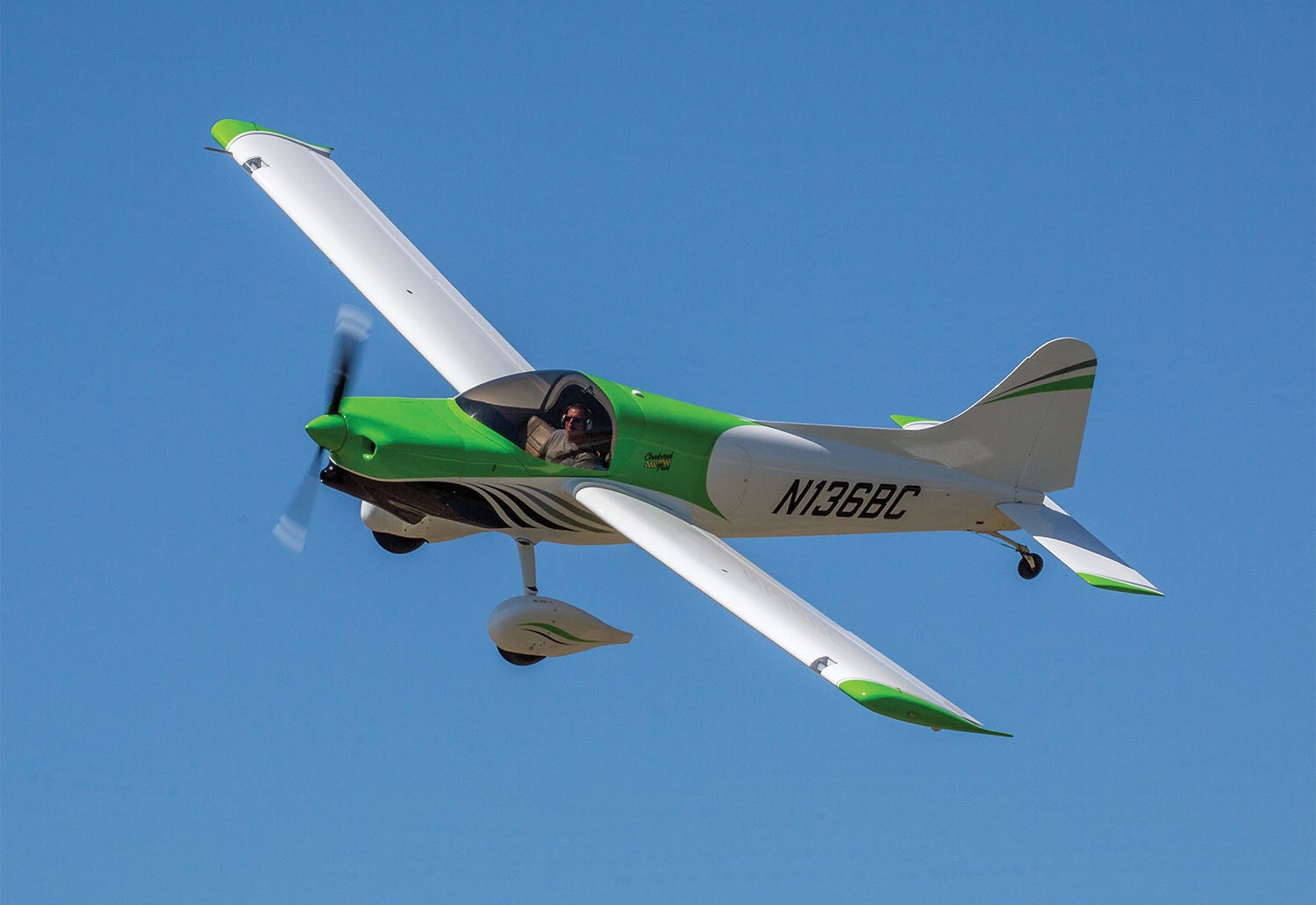
The son of a pilot, Bounds has been an airplane nut since childhood, but he didn’t learn to fly until 1983–84, after he met his wife. “Here was this tall, good looking girl, and her dad had an airplane,” a Cessna Cardinal that he rented to Bounds “for $25 an hour, wet!”
His instructor was “a starving spray pilot” who’d just started his business. “He got paid by the acre, so my wife basically fed him that winter and he taught me to fly for free. He was death on handling the airplane. We did accelerated stalls and spins and all the stuff you don’t have to do [to earn a private pilot certificate].”
Completing the Bearcoupe’s Phase 1 testing, “I did some backcountry flying hither and yon.” On its inaugural visit to Oshkosh in 2014, Bounds earned an Outstanding Workmanship award. “I think that was because I was in a sea of RVs. The judge came by and said, ‘I don’t know what in hell this thing is, but it ought to win something,’” Bounds said, chuckling. “I was pretty swelled up about that.”
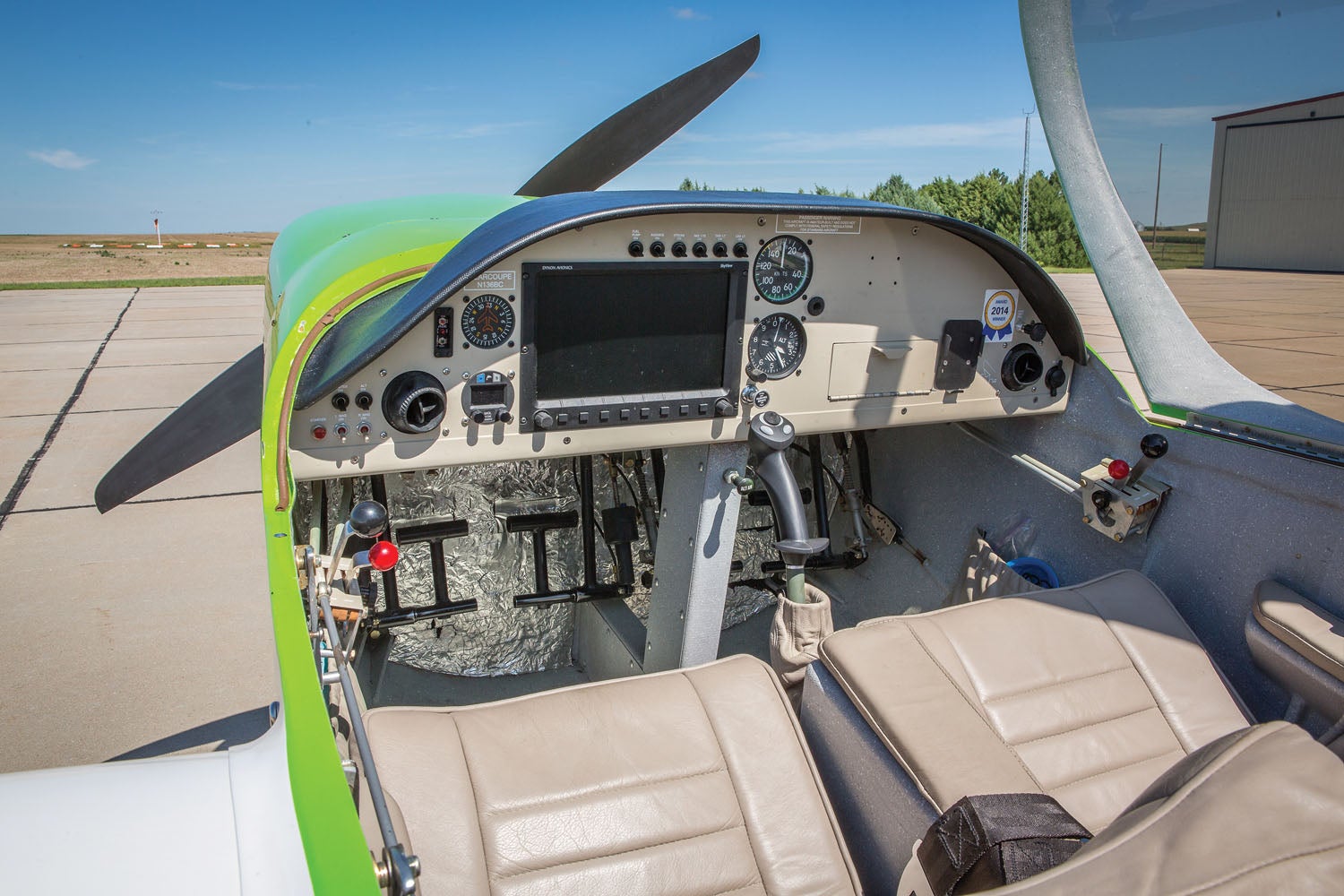
A Generally Bad Day
A prudent pilot, when venturing into a new backcountry region, Bounds flies first with an instructor who knows the area. The 13,000-hour CFI he flew with in Hanksville, Utah, “knew his stuff.” Returning to the airport, “where I was going to drop him off and get my wife to show her some of the backcountry strips we’d just been to, he asked if he could land,” Bounds said.

“My son is tall and has really long feet, so the rudder pedals on the right side are high up and hinge at the top. This guy was short, and he didn’t like the way the pedals felt, so he slid his feet up on the brakes. When we touched down, he had the brakes locked and—wham!—we went right over.”
The Catto prop “made a few ditches in the berm,” said Bounds. “It wasn’t broken, so I sent it to Catto, asking them to take a look at it. They asked what happened, and I told them I flipped the airplane and stuffed it in the dirt. After examining it, they said it was OK, so they put new leading edges on it, refinished it, sent it back,” and he put it on the Lycoming, which had undergone its own examination.
The rest of the airframe didn’t fare so well, he said. “It tore the cowl off, destroyed the canopy, crushed the turtle deck a bit and the tail halfway. One wingtip was caved in, and it was skinned up here and there. The wheels and tires were fine.”
With unexpected understatement, Bounds said, “It was, generally, a bad day.” The shoulder harness broke Bounds’s left collarbone and arm, “and I’m left handed.” Because the instructor evidently didn’t get his harness fully latched, he slid forward and broke his neck.
Like the Defiant and Prospector, the Bearcoupe’s canopy swings to the side. Hinged on the right, the occupants enter the cockpit by climbing two steps on the left gear leg, sit on the wing and swing their legs into the cockpit.
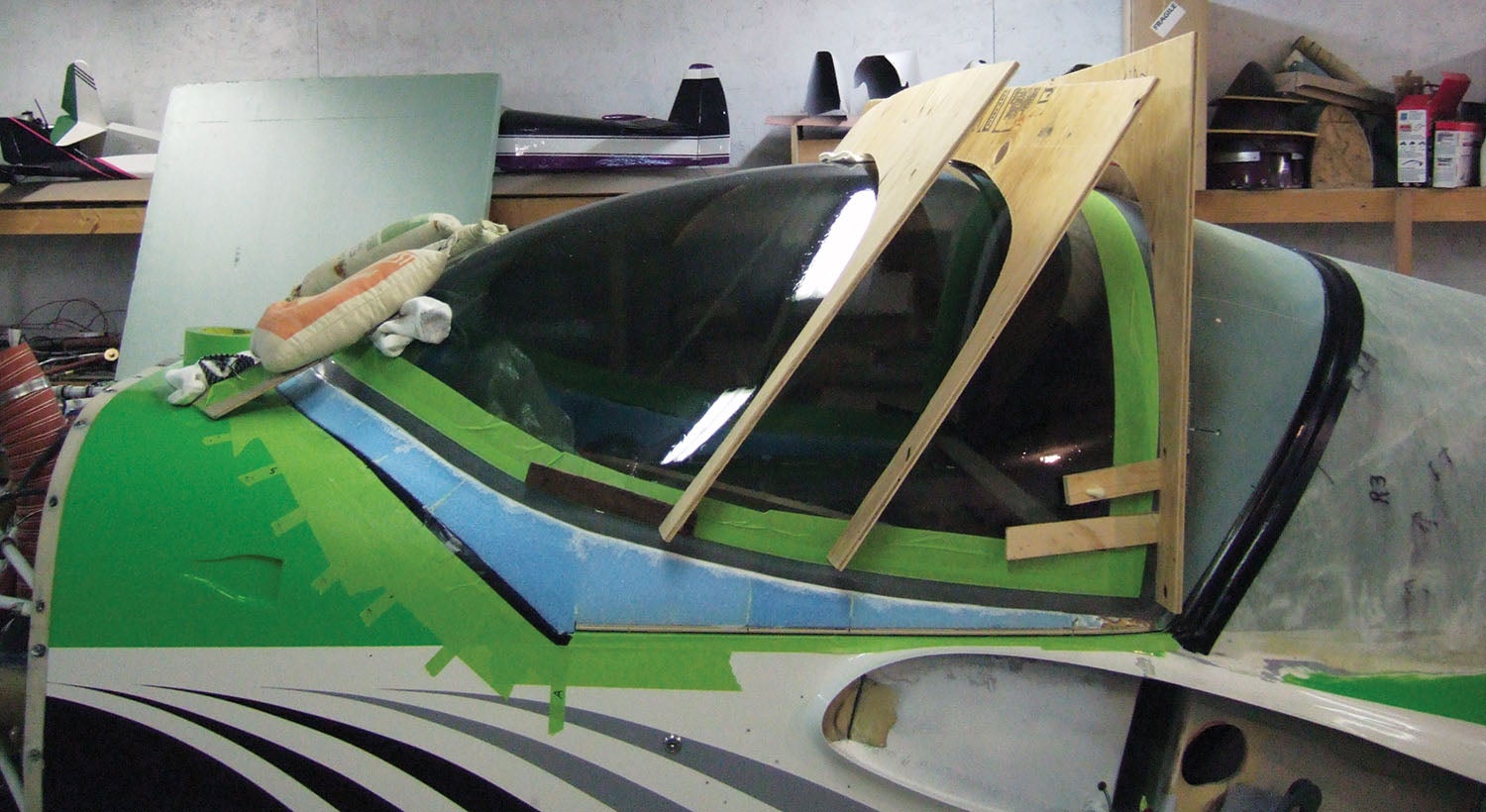
To provide a way out in case of a rollover, Keller kept the cockpit open above the spar and put an oversize baggage door behind the left wing. This was prescient because Keller flipped the Prospector at Oshkosh 1989 (where it was named grand champion) when an inaccurate fuel sight gauge resulted in a surprised silence during a photo flight that ended upside down in a wheat field.
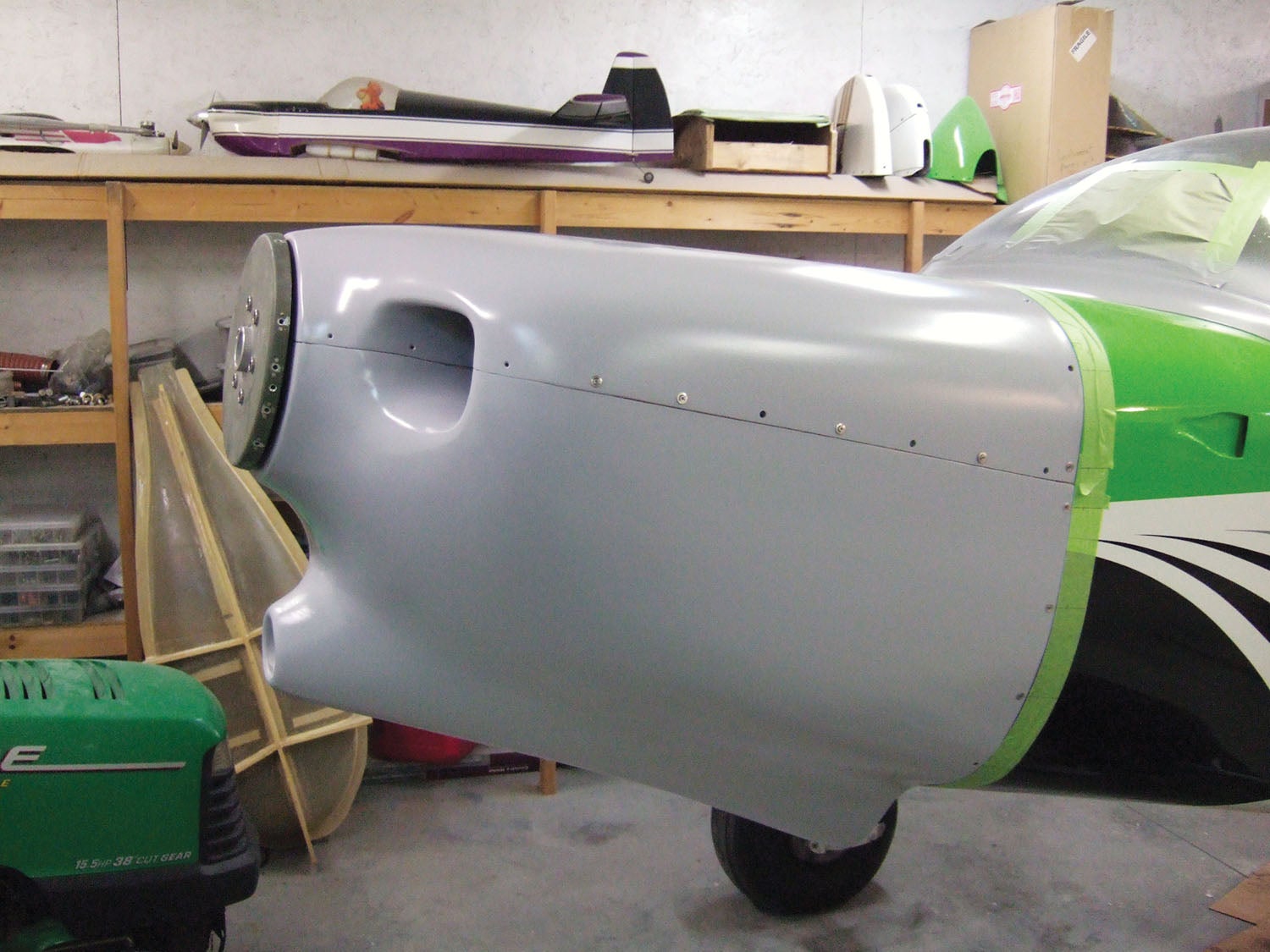
Bounds didn’t have the Keller-designed latch that also opened from the inside, and he wasn’t interested in causing more damage by kicking out the baggage door, so he removed the latch with his Leatherman tool.
By the time he’d wiggled out of the baggage door, people were coming to their rescue. They lifted the Bearcoupe by a wingtip and the EMTs in the group carefully extricated the instructor. Located just north of Lake Powell, Bounds said they have an excellent EMT group there because “a lot of visiting desert riders get hurt…and it is 115 miles to the nearest hospital.”
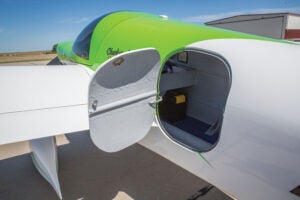
At the hospital, Bounds said he was in a panic. “After getting fixed up, I had to get back and get the airplane off the runway, and I didn’t know how I was going to do that in the middle of nowhere. When I got to the airport, the airplane was sitting on the ramp. The nephew of one of the guys ran a crane service, so they went out and flipped it over without doing any more damage to it that I could tell.”
After returning home, he and three friends pulled a trailer 600 miles to collect the Bearcoupe. “We put it in the shop and started on it again.” His wife was an essential member of the reconstruction crew. “She’s a grumpy, really good fiberglasser. I get mad and ready to pull my hair out and throw stuff. And she just stands there, like, OK, when you calm down, let’s get going.” But she made it clear that “my next wife can help me with my next airplane.”
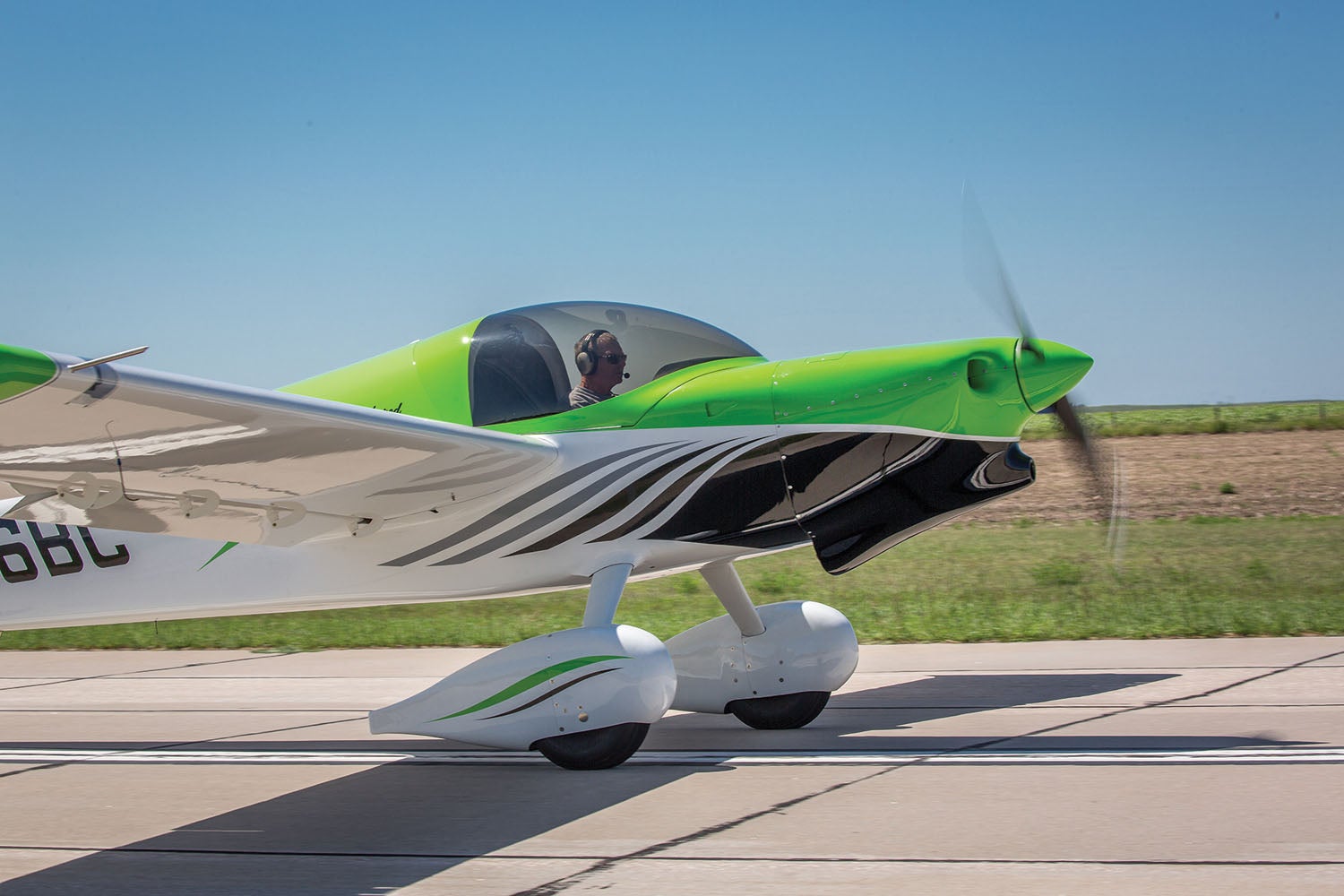
Reconstruction consumed two years, he said, and the hardest parts were the cowling and canopy. “A guy in Florida blew the canopy as a big bubble and then cut it in half,” Bounds said. “He sold me the canopy for $500 and offered me the other half for $200, saying it would fit no other airplane. If I wanted it, he said he’d ship it with my canopy, and I said you betcha! So I had a spare canopy sitting in my shop for a couple of years. How’s that for lucky? Of course, I still had to make a frame for it.”
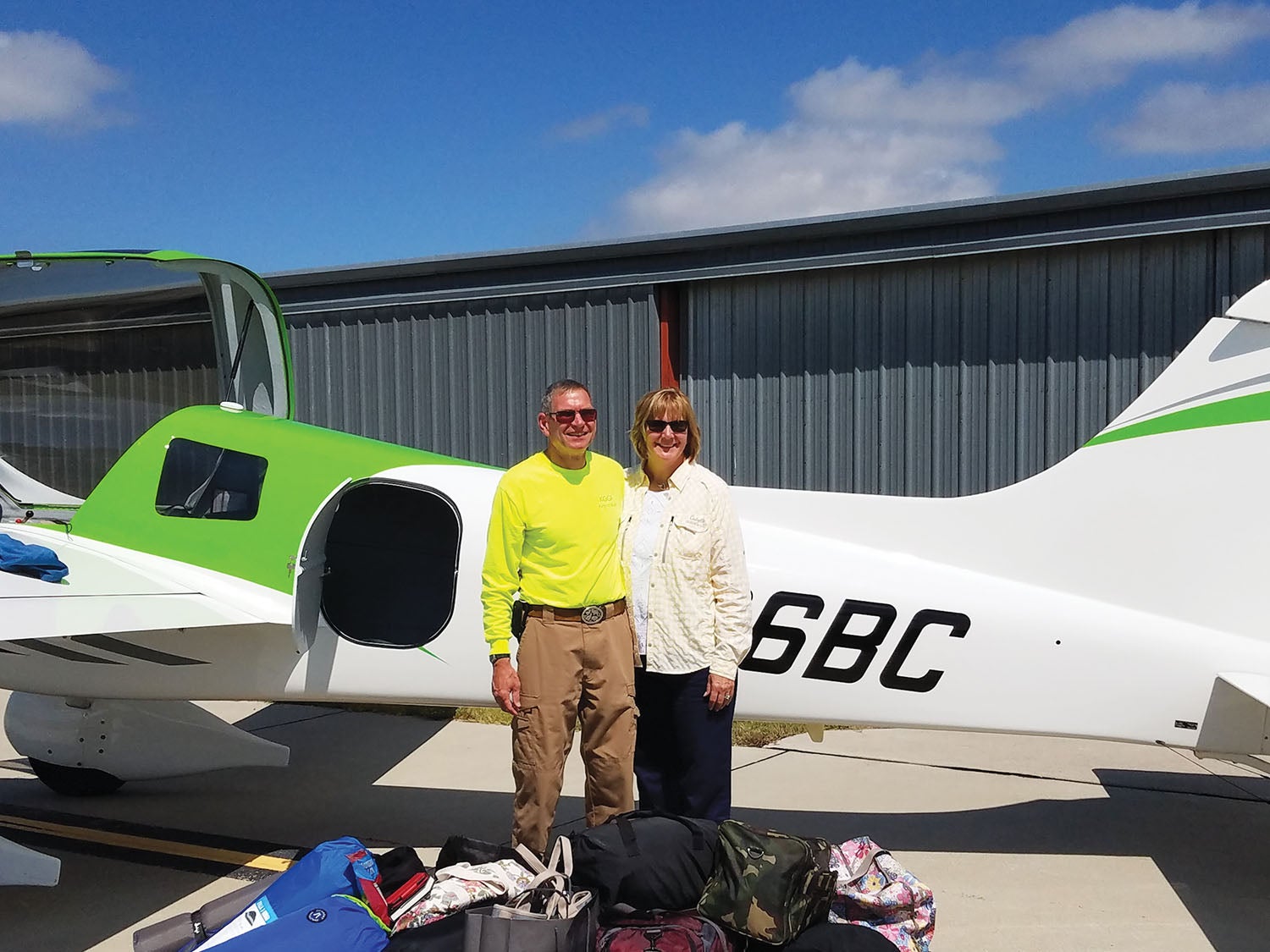
Since its rebuild, Bounds and his wife have made a number of happy Bearcoupe trips to the backcountry and beyond. And every trip recreates the miracle of the Bearcoupe’s first flight and the ineffable joy that its unusual gestation worked out OK.
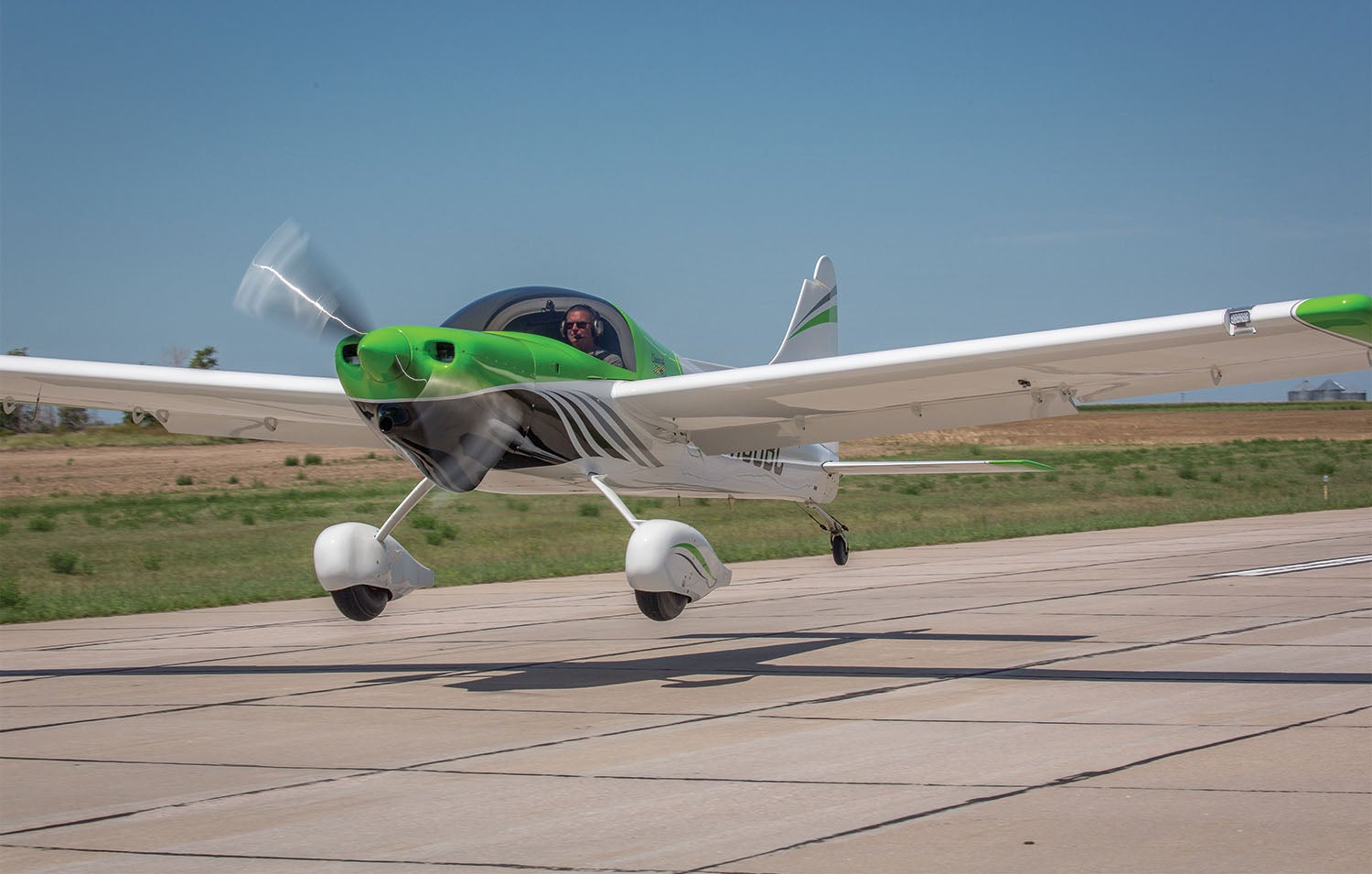
Photos: Bob Bounds and Scott Spangler.
Lovely article. I really enjoy reading about different and individual projects. Did the instructor recover well?
Beautiful bird that was given a LOT of thought to off-airport work. As a long-time C-180 owner, this bird is downright attractive. I think it makes a wonderful addition to the back-country genre. I especially like his baggage door ideas.
Yes, the instructor recovered and returned to the sky.
Hi Scott,
If I may ask, where did you get the green paint? So difficult to find a green that “pops” like that. I have been told by local paint suppliers (here in South Africa) that that a bright deep green (like yours) is not available as a 2K type paint (the closest they come to the green I want is something called “Kawasaki Green” which is still quite dull. They do however have a fluorescent green that is perfect but I am told does not last very long at all in sunlight.
When the green was laid down, was is over a white base? Any other clever tricks?
Thanking you in advance,
Gary Glasson
Glad to read the Lycon rebuild of the 340 wasn’t mentioned as a problem. I had a Cato three blade on it when I made my last Lancair flight. I believe Cato could have repaired the three shortened blades, loved the prop. Stopped flying after my annual inspection failed to detect a crack in the engine mount that caused the nose gear to fail to lower.