For the past few editions of Wind Tunnel, we’ve been exploring the factors that drive the configuration and placement of landing gear. Last month we took a look at the factors affecting the directional stability and lateral stability of the airplane when it is rolling on the ground. This month we switch axes to look at the longitudinal effects of the landing gear configuration.
The primary decision the designer must make is the fore and aft position of the main wheels relative to the CG. This decision involves multiple factors including ground operations and takeoff and landing behavior.
Tricycle gear and taildragger gear are affected differently in this area because of the fundamental difference in layout. On a trike, the main gear is located aft of the CG, and significant weight is borne by the nose gear while the airplane is on the ground. On a taildragger, the mains are ahead of the CG, and the tailwheel is relatively lightly loaded. Let’s get started by take a closer look at tricycle gear.
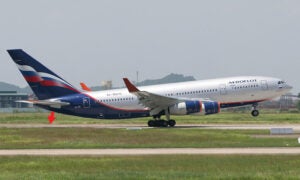
Taxi
When a tri-gear airplane is taxiing, it is in a relatively level attitude with all three wheels in contact with the ground. The percentage of the weight of the airplane carried by the nosewheel is determined by how far the main gear is aft of the CG.
On the ground, it is desirable to have a bit of load on the nose gear. Many airplanes have steerable nose gear, and the ability of the nosewheel to steer the airplane on the ground is determined by how much traction it has. If the load is too low, the nosewheel can skid relatively easily and the airplane will not turn as commanded by the nose gear. This is not an issue on a configuration with a castering nose gear since the nose gear cannot steer the airplane. All steering for this configuration is done with a combination of differential brakes and the rudder of the airplane. Which does what is a function of airspeed: At low speed the brakes are the primary steering mechanism. As speed increases (typically on a takeoff roll), the rudder takes over.
Another concern if the mains are too far forward is the behavior of the airplane when taxiing over bumps in the surface. If the load on the nose gear is too low, the bump may cause the airplane to rock back, and the nose gear to leave the ground. This “hobbyhorse” motion is extremely undesirable and should be avoided.
Takeoff
The most important factor in determining the position of the main gear on a tricycle landing gear is takeoff. As the airplane accelerates down the runway, the pilot must be able to rotate the airplane nose-up, lifting the nose gear off of the ground to establish a positive angle of attack for liftoff.
It is very important that the minimum airspeed for nosewheel liftoff be well below the liftoff speed of the airplane.
For a safe takeoff, the pilot must be able to smoothly rotate to and capture the proper attitude for liftoff. This is a fundamentally unstable situation because as the airplane rotates, load shifts from the main wheels to the wings. Since the main wheels are behind the CG, load on the mains produces a nose-down moment about the CG of the airplane. Unloading the main gear produces a nose-up shift in pitching moment that accelerates the rotation.
The farther aft of the CG the main gear is, the more unstable the rotation is. If the main gear is too far aft, the pilot will not be able to start the rotation at, or slightly below, the desired liftoff speed and rotate smoothly. Instead, the airplane will initially refuse to rotate, even with a large nose-up elevator deflection. At some critical airspeed, the elevators will finally have enough authority to lift the nose. At this point, things can start to happen very quickly. As the airplane rotates nose-up and unloads the mains, the large nose-down moment from the main gear goes away quickly, particularly if the airspeed is well above stall. The combination of this and the large initial elevator input required to start the rotation will cause the airplane to pitch up rapidly and the nose-up pitch rate to accelerate. The pilot will have to counter this with significant nose-down stick input to capture liftoff attitude and not over-rotate.
In extreme cases the airplane will jump into the air with a rapidly increasing nose-up pitch rate. This “hop-off” phenomenon is extremely dangerous and has caused multiple accidents in early testing, particularly of unconventional airplanes. A common accident scenario is a high-speed taxi test where the pilot gets the airplane going fast but does not intend to lift off. A large up elevator deflection, usually due to an attempt to rotate, causes the sequence to start and will catch the pilot by surprise. The airplane rotates rapidly nose-up, jumps into the air in a very nose-up attitude, stalls and falls back down, usually with unpleasant consequences.
In early testing of a new design, it is vitally important to establish the ability to lift the nose gear at an airspeed below stall speed. Some certification standards require positive nose-gear liftoff at no more than 85% of stall speed. This is a good guideline for safe rotation characteristics.
Under no circumstances should a taxi test allow the airplane to exceed stall speed on the ground until the ability to rotate smoothly and under control at airspeeds below stall has been established. If the airplane refuses to rotate, do not increase speed trying to make it do so. If the airplane won’t rotate at an acceptably low speed, it’s time to do the analysis of why and make appropriate modifications. Pushing on to higher airspeed trying to make the plane rotate is very dangerous and has killed more than one overly aggressive test pilot.
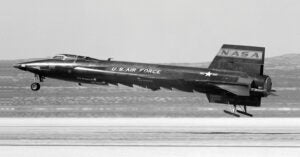
Landing
On landing, a tricycle-gear airplane touches down first on the main gear. As airspeed decays, the airplane rotates nose-down to bring the nose gear down. After the nose gear is rolling, the pilot can apply braking to slow the airplane.
As with takeoff, it is desirable for the pilot to be able to control the rotation. On most airplanes, the pilot has the option of holding the stick back and letting the nose gear settle to the runway as airspeed decays and the elevator loses authority, or relaxing back pressure after touchdown to fly the nose gear down to the runway.
As with takeoff, landing favors a more forward position of the main gear to give the pilot the maximum control of the attitude of the airplane during the transition from flight to rolling on the ground.
If the mains are too far back, the elevators will not be able to prevent nose-down rotation after touchdown and keep the rotation rate low enough to have the nose gear gently touch the ground. This “slap-down” of the nose gear is very undesirable and can lead to damage to the airplane. An extreme case of this showed up on the experimental X-15 rocket plane. The X-15 was air-launched, so it did not have to rotate for takeoff. It had a trike gear with skids for the main gear and a steerable nosewheel. The skids were integrated far aft on the airplane to keep them clear of the fuel tanks that comprised most of the fuselage, so the airplane would rotate nose-down rapidly as soon as the main skids touched down. On one heavyweight landing, the combination of the higher weight and higher sink rate caused the airplane to rotate nose-down so rapidly that when the nose gear hit, it broke the fuselage in the middle.
Main Gear Position
Overall, most considerations tend to drive the main gear forward. Light loads on the nose gear make the airplane more controllable on both takeoff and landing, and reduce stress on the nose gear itself.
The mains should be far enough back to allow good nose-gear steering and prevent hobbyhorsing while taxiing, but not farther aft than that unless some other consideration strongly dictates that the mains move aft.
A good rule of thumb for preliminary design is to place the contact point of the main gear at a point determined by the intersection of the ground and a line through the CG inclined 15 degrees off of vertical. This means that if the airplane is rotated nose-up 15 degrees on the main gear, the CG will be exactly over the contact point of the wheels on the ground. Use this as a starting point position for the gear and then, as the design progresses, do the analysis of nose-gear liftoff speed to refine this position.
I’ve run out of space for this month, so next time we’ll cover static ground attitude for trikes and then move on to main gear positioning for taildraggers.