Of the four major forces of flight, none keeps the typical homebuilder awake at night more than thrust. After all, gravity is God-given and drag appears automatically. Lift must be generated by building wings, but thrust comes only after a seemingly endless circle of engineering compromises and intertwined consequences. It can cost a ton of money, and the choices made in those sleepless hours have performance and financial consequences that last the life of the airplane.
In short, no other single component of the building experience costs so much or has such a profound effect on the airplane’s personality and performance as its engine. And beyond the science of converting 100LL into a lot of noise and some thrust, there are the man-made considerations such as warranties and resale values and perhaps the psychological tug of a “free” core engine hiding in the back of some hangar.
In this buyer’s guide, we’re skipping over the engineering of deciding which engine is best for your airframe and flying direct to the commercial realities of what engines are available. In some ways it’s a wide field, with certified airplane engines at one end and auto conversions at another. This month we’re examining the traditional aircraft-engine market, the familiar Continentals and Lycomings, along with their aftermarket clones, plus engines that are becoming increasingly popular in the Light Sport Aircraft realm, and the vestigial radial offerings. Next month, we’ll present the alternative auto-engine conversions and cottage-industry specialty designs for those with a tinkerer’s heart.
State of the Market
Viewed from afar, the traditional airplane piston-engine business is a lonely hamlet hanging on to the old ways at the edge of the woods. For mainstream kit builders, there are but two manufacturers that have dominated, Continental and Lycoming, and their expected bread and butter—new engine sales to big airframe manufacturers such as Cessna and Piper—trickle along, but don’t have the flow to drive major innovations such as all-new engines. Compared to the frantic rush in the electronic, automotive and medical industries, the pace of progress in piston engines is glacial, chained by an unresponsive regulatory climate and market demand stymied by a shrinking pilot population and an uncertain world economy.
Now that we’ve cheered you up, let’s just say that we don’t want to blow a lot of smoke about exciting breakthroughs just around the corner. Yes, government drone development may spiral down to general aviation eventually, and a healthy number of evolutionary improvements are coming to market, but nothing revolutionary is popping out of the clouds. In a way this is comforting, for unlike avionics purchases, your 200-horsepower, four-cylinder powerplant won’t be going out of date anytime soon. Even considering the 100LL fuel availability question, there’s no reason an engine bought in 2013 shouldn’t be swinging a propeller long into the future.
If there’s any upside to the brutal market, it’s been cleansing in the same gentle way a warehouse fire clears out old inventory. Most of the marginal shops—and unfortunately some of the good ones, such as Mattituck—have closed since the economy faltered. What’s left in the Experimental Continental and Lycoming engine business are mainly the more-established, better-equipped shops with a history of both performance engines and a good base of certified overhauls.
And let’s not forget that while Continentals and Lycomings may be traditional, they are intelligently designed, highly developed and robustly rebuildable. It’s essentially impossible to beat these engines in the 200- to 350-hp range. For less than that, Rotax rules in Light Sport Aircraft, and UL Power is making a strong bid.
Kit, Complete, Overhauled or Certified
Traditional Continental and Lycoming aircraft engines can be broadly categorized as either certified or Experimental units. The certified engines (and propeller combinations) are exactly what they sound like: FAA-recognized engine and prop combinations fitted to certified airplanes. When transferred to Experimental aircraft, certified engine and prop combinations have the advantage of, well, not being so experimental. Unfavorable harmonic speed ranges and other lurking demons uncovered only by thorough engineering are known and addressed with certified powerplants, meaning you don’t have to play test pilot quite as convincingly. The FAA recognizes this advantage by requiring a shorter flight-test phase for certified installations, typically 25 hours instead of 40 hours for Experimental engines. Later on, you’ll find a certified combination is a good thing at resale time.
Not surprisingly, buying a new certified engine and prop combination is a bracing splash of financial ice water, and is not the most commonly exercised option. Sourcing a timed-out certified combination in the classified ads is perhaps more common, though good core engines are not as plentiful as they once were. But if you have a good core, it can be rebuilt to certified standards to preserve its certified status; modify it, and it becomes just another Experimental engine.
For those building a well-proven design—an RV comes immediately to mind—there is little experimental in the finished airplane when fitting a certified engine and prop combination. Such planes cost more initially but shouldn’t require anything more than regular maintenance, and they boast good resale value because in many people’s minds they are technically equivalent to the most proven certified airplanes. Van’s reports that most of its customers purchase new engines through Van’s, while some international customers are forced to purchase new certified engines due to regulations in their home countries.
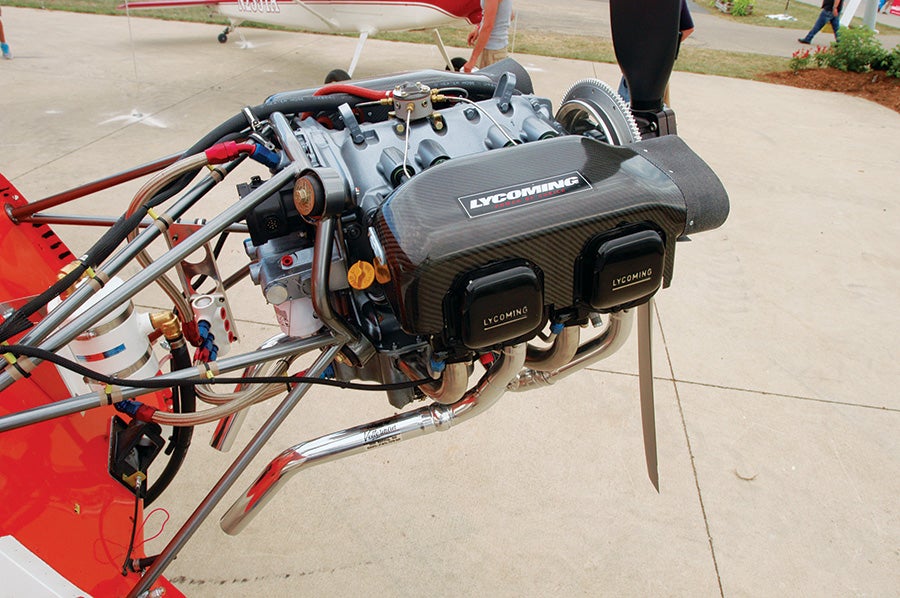
Lycoming’s Thunderbolt line begins with the 233, seen here in 120-hp, AEIO-233-EXP trim on an FK12 Comet biplane. At the other end, Thunderbolts range up to 400-hp, eight-cylinder IO-720s.
Something to remember when going the certified route is that aside from oil and spark-plug changes, a kit builder with repairman’s privileges can’t legally maintain such an engine. And, as just noted, any modifications at any time, even long after the airplane is flying, must have an STC—or the engine changes to an Experimental.
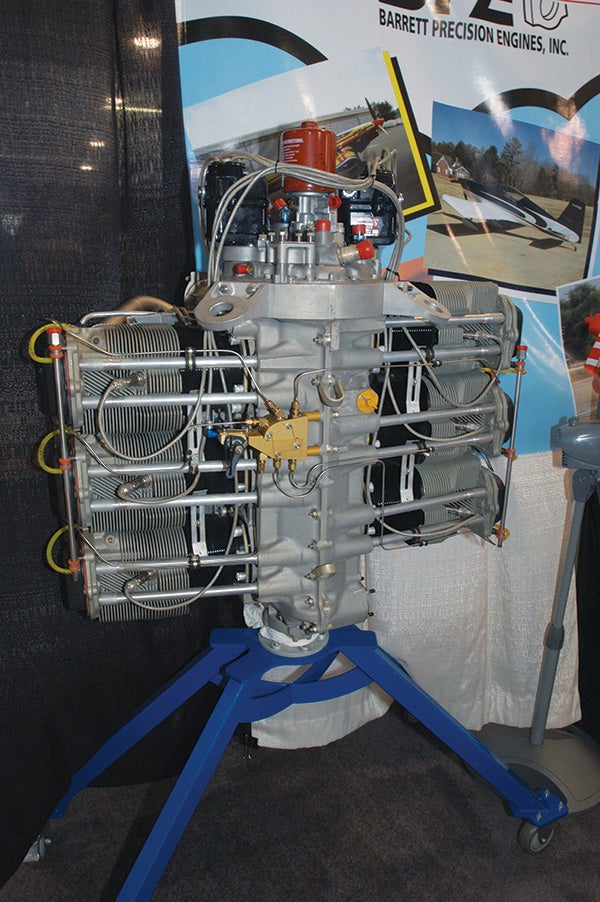
Builders interested in the 225- to 400-hp range gravitate toward six-cylinder Continentals and Lycomings. Almost to a one, these engines are built by private engine-overhaul shops, such as this IO-540-EXP Lycoming from Barrett Precision Engines.
Not certified, but certainly familiar, are aftermarket versions of the 320 and 360 Lycomings. Such EXP “clone” engines can actually come from Lycoming in the case of its Thunderbolt line, or just as easily from ECi (Engine Components International) or Superior. Sometimes these clones differ from certified engines only in their paperwork because the component parts are all certified.
Furthermore, these clone engines are also typically sold disassembled as kits. The idea is that everything required to assemble a new engine is delivered at one time, saving the hassle of separately sourcing every bolt and washer, then verifying each part, rebuilding what’s usable and replacing what isn’t. Such kits may seem expensive at first, but they can be a huge timesaver.
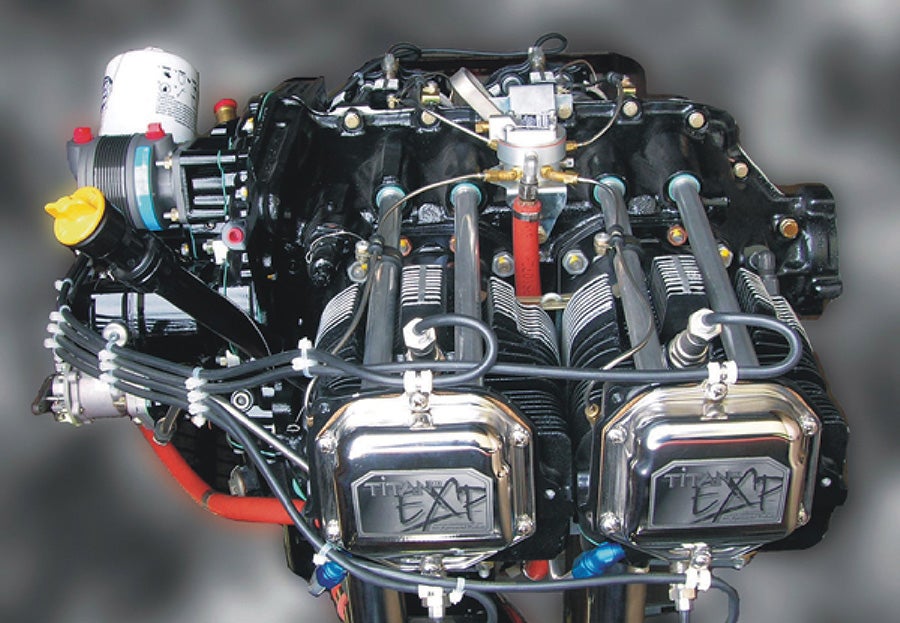
ECi uses the Titan brand name, most famously for its cylinders, but also for its Experimental engines such as this IOX-360 Titan EXP.
In fact, the time and hassle savings are so great that in a few instances where all of the clone parts are certified, shops can “rebuild” an original certified Lycoming by removing its data plate and attaching it to a new clone engine. It’s no different than if the parts had been sourced separately, and everyone saves a bunch of time. It’s certainly a quick way to return to new tolerances and upgrade to roller lifters.

Experimental engine shops say approximately 80% of their business is for 360 Lycomings, and, naturally, most of those are going into RVs. This Aero Sport Power IO-360-M2S, destined for John Tierney’s RV-7A, is about as typical as they come.
Getting back to the disassembled kits, we’ll note the number of engine kits screwed together in homebuilders’ garages is tiny. More typically, builders order the kit engines through an engine shop, which then does the assembly. That’s probably a smart idea for all but the most experienced amateur builders.
Yet another option, just developing at our press time, was a kit engine-build school Superior is considering. Like builder-assistance workshops from airframe builders, the assisted engine assembly would join your labor and the engine manufacturer’s knowledge and facilities in a compelling combination of education, lower cost and time savings.
Curiously, over the last year or so Lycoming may have priced itself out of the kit engine business. Shop owners report they can rebuild a core engine, build an engine from their existing core stockpile, or use an ECi or Superior kit for considerably less than going with a Lycoming kit. Lycoming’s Thunderbolt engine line remains competitive, so perhaps the company just wants control over assembling the engines.
Once past the certified and clone engines, there is the option of custom building an Experimental engine using any combination of OEM and aftermarket parts. This is a popular path for those wanting something special, such as racers, aerobatic competitors and the power-jaded, as well as those whose engine shop can put together a nice powerplant from their parts pile for a competitive price. This is also popular with parts scroungers and traders who have accumulated a pile of core engines or components; they can trade in parts to an engine shop, along with some money, and come out with a traditionally based Experimental engine for relatively little cash.
Ly-Con says most of its Experimental customers these days choose to buy a core engine from Ly-Con rather supply their own. It’s simple economics: The Ly-Con core has a known, set price (around $5,000-$6,000). But when the customer supplies the core, there are often expensive surprises inside, and in any event, insisting on rebuilding the exact engine you walked in with will almost always slow down the process, even if there is nothing other than normal wear.
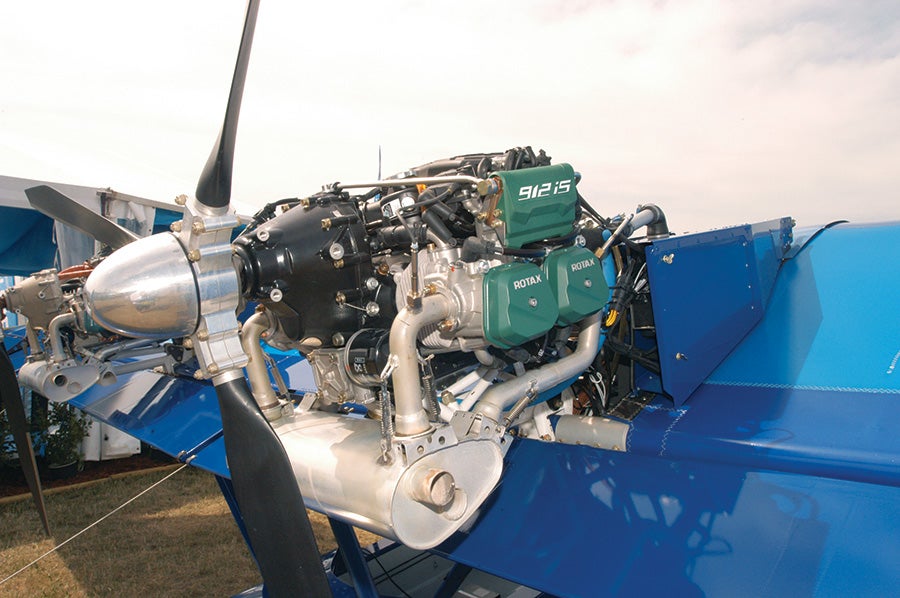
Rotax’s 912 iS has all the electronic injection and engine controls the market says it’s been waiting for. We’ll see how many are ready to pay for all this goodness.
Engine Trends
Although development is slow, there is still a demand from buyers for better fuel economy and especially for more power (what else is new?), and the industry is working hard to respond. For several years, the main talking point from Lycoming and Continental has been roller cams. This more-efficient technology is now well implemented in new engines, and the custom rebuild shops have developed their own take on retrofitting roller lifters to existing engines, so there’s little need to do without them.
What roller lifters do is reduce friction between the highly stressed cam lobe and lifter for a resulting gain in efficiency. A secondary, but still welcome, advantage is that roller cams are less susceptible to damage from corrosion caused by the number one killer of airplane engines, inactivity.
Another significant bump in efficiency comes from the movement by the more experimental among us to higher compression ratios. This isn’t Lycoming’s and Continental’s favorite subject, as they view the increased stress on fundamental engine parts such as the pistons, rods, crankshaft, bearings and case as outside of their comfort zone, but the custom shops have broad experience with 9.5 and 10:1 compression ratios and they’re not losing any sleep over it. There’s no consensus whether these bumps in compression reduce the time between overhauls. Some shops say TBO is unaffected, while others disagree by an unspecified amount, which we take to mean several hundred hours, so that’s something to discuss with your engine builder. On the other hand, the increase in performance is indisputable, especially for those cruising in the 7000 and up altitudes. The gain in speed, climb and fuel economy at altitude makes a bit of compression the poor man’s turbo-normalizing.
Very much part of the Experimental engine scene today is increased displacement. This trend has no clear-cut impetus behind it, say the engine shops, other than the general trend toward more horsepower. As always, there is no replacement for displacement when it comes to making power, as a few more cubic inches are almost always the least expensive, most dependable route to increased power. The extra inches are coming mainly from longer-stroke crankshafts, as the cylinder bores are already at their maximum in most aircraft engines. The poster child for the breed is the 360 Lycoming, stretched to a tad over 400 inches, though there are definitely other combinations available.
There are several meaningful advantages to stroker engines, not the least being the bigger engines fit in the original engine’s footprint, so there is no need to enlarge the cowling, change the cooling baffling or deal with other fitment issues. Furthermore, the larger-displacement engines gain little weight in the processes, so performance isn’t compromised by increased mass.
The downsides are that strokers cost more and drink a little more fuel, so big displacement is more of a power grab than an increase in efficiency. Interestingly, the shops report no loss in TBO due to the larger power pulses. After all, in a typical 400+-cubic-inch four cylinder, each cylinder is a little over 102 cubic inches, or the displacement of an entire economy-car engine. That’s a lot of bang per power stroke.
As recently reported in KITPLANES® (March 2013 issue), one fallout from the Red Bull air races was a movement to lighten aircraft engines by trimming excess weight from internal parts such as pistons and pins, along with cutting of unneeded bosses, lightening flanges and using lighter-weight accessories. The Red Bull competitors were looking for snappier turning, but aerobatic and backcountry pilots appreciate the overall increase in performance too.
Buying an Engine
Engine manufacturers and rebuild shops say the majority of complete Experimental engine purchases are by kit aircraft builders, which logically leads to the airframe kit manufacturer as the source for engines. In fact, Lycoming, which embraces the Experimental engine market, has specific part numbers for several of the more popular kit planes. Lycoming labels these specific engines OEM Experimentals because they are, in essence, the Original Equipment Manufacturer engine for that kit aircraft, yet are Experimental engines as far as the FAA is concerned.
In the lead in this regard is Van’s Aircraft, which makes engine selection as easy as ticking off another box on the order form. This is often a cost-effective decision because the engine is guaranteed to be correct for the airframe. The aggravation and time lost to chasing down small parts, or dealing with difficult-to-foresee surprises, such as a magneto that wants to be in the same place as an engine-mount tube, are avoided, and generally life goes much more smoothly.
Thanks to its high volume, Van’s can offer competitive pricing on both certified and Experimental engines. And as you’d expect, Van’s, Glasair and other kit makers are excellent sources to consult when it comes to selecting accessories such as induction and exhaust because they know what fits their engine mounts and airframes.
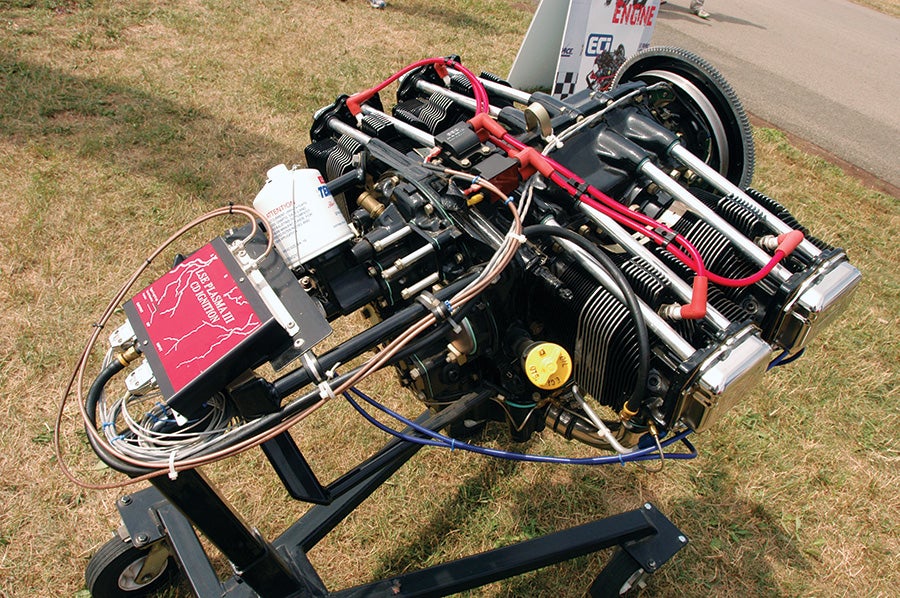
Experimental engines all offer long option lists for things such as custom paint, electronic ignitions and higher compression ratios. Typical of the breed is this OX-360 Titan on display at AirVenture.
Otherwise, the traditional path to engine ownership is an engine shop such as Aero Sport Power, Barrett Precision Engines, Eagle Engines and Ly-Con Aircraft Engines, to name a few. These specialists are dealers for the two OEMs, plus the ECi and Superior lines (often for all four), plus they offer a wealth of knowledge about what works, what doesn’t and what’s cost effective. Also, most are dealers for accessories such as starters, magnetos, etc., and can handle custom installations and accessory service long after the initial engine sale. These shops are where the innovations such as adjustable oil-pressure relief valves and cold air intakes come from too. In short, if it’s firewall forward, these guys know what’s up.
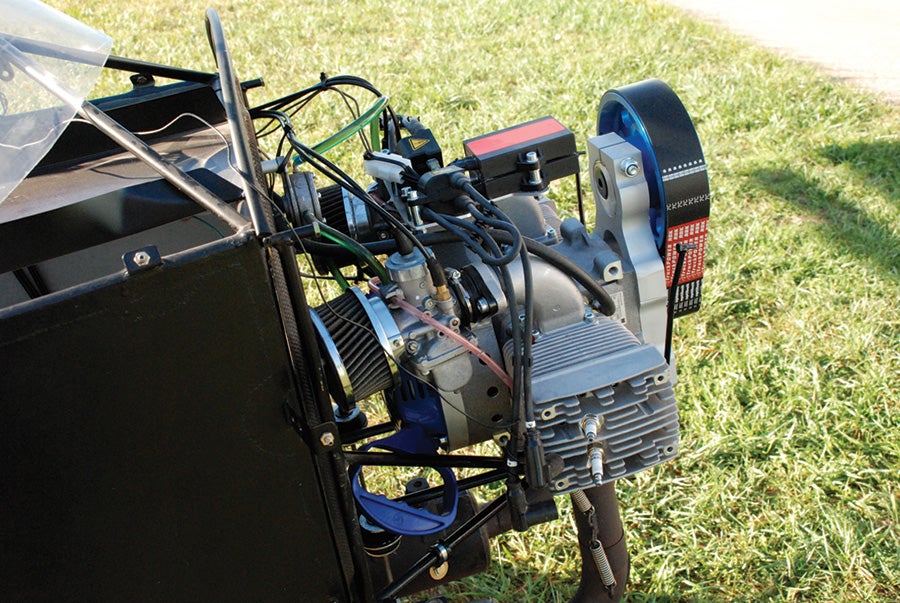
The Hirth F-23 50-hp two-cycle. Recreational Power offers a variety of engines for light aircraft, all with AI-Nikasil coated cylinders.
Another major plus for an engine shop is engine break-in. For our money and hide, the $1,000 it typically takes to have your engine installed on a dyno and run-in by a pro is the best insurance policy going. It allows for making that first flight knowing it isn’t your engine’s first time running, it isn’t leaking, infant mortality isn’t lurking in the magnetos or carburetor, and above all, it frees the test pilot from the overwhelming task of simultaneously evaluating a new airframe and breaking in a new engine. Traditional aircraft engines hate low-power operation during run-in—it’s begging for glazed cylinders—yet do you really want to blast around in your new speedster at a minimum of 75% power on the first flight? Half a day on the engine dyno means your powerplant has a good start on break-in and already has its first oil analysis done before the tires leave the runway.
It’s guaranteed you’ll want the engine on the airframe long before the first flight to install systems and fit the cowling, and that means a long time between the engine dyno and first flight. To avoid corrosion, have the engine shop “pickle” the engine with preservative oils.
Still Cloudy, But No Turbulence
After transiting several years of nasty economic cumulonimbus, the recent stability and occasional modest profitability reported by traditional engine makers is comforting. Likewise, Lycoming’s drone business bodes well for electronic engine controls actually debuting from the OEM giant.
In the meantime, Rotax and UL Power are already there. They look to mark 2013 as the breakout year for electronics in Light Sport and compact two-seat sport planes. One wonders how long it might take the higher-powered examples of these engines to move into the Van’s Air Force heart of the kit-building movement?