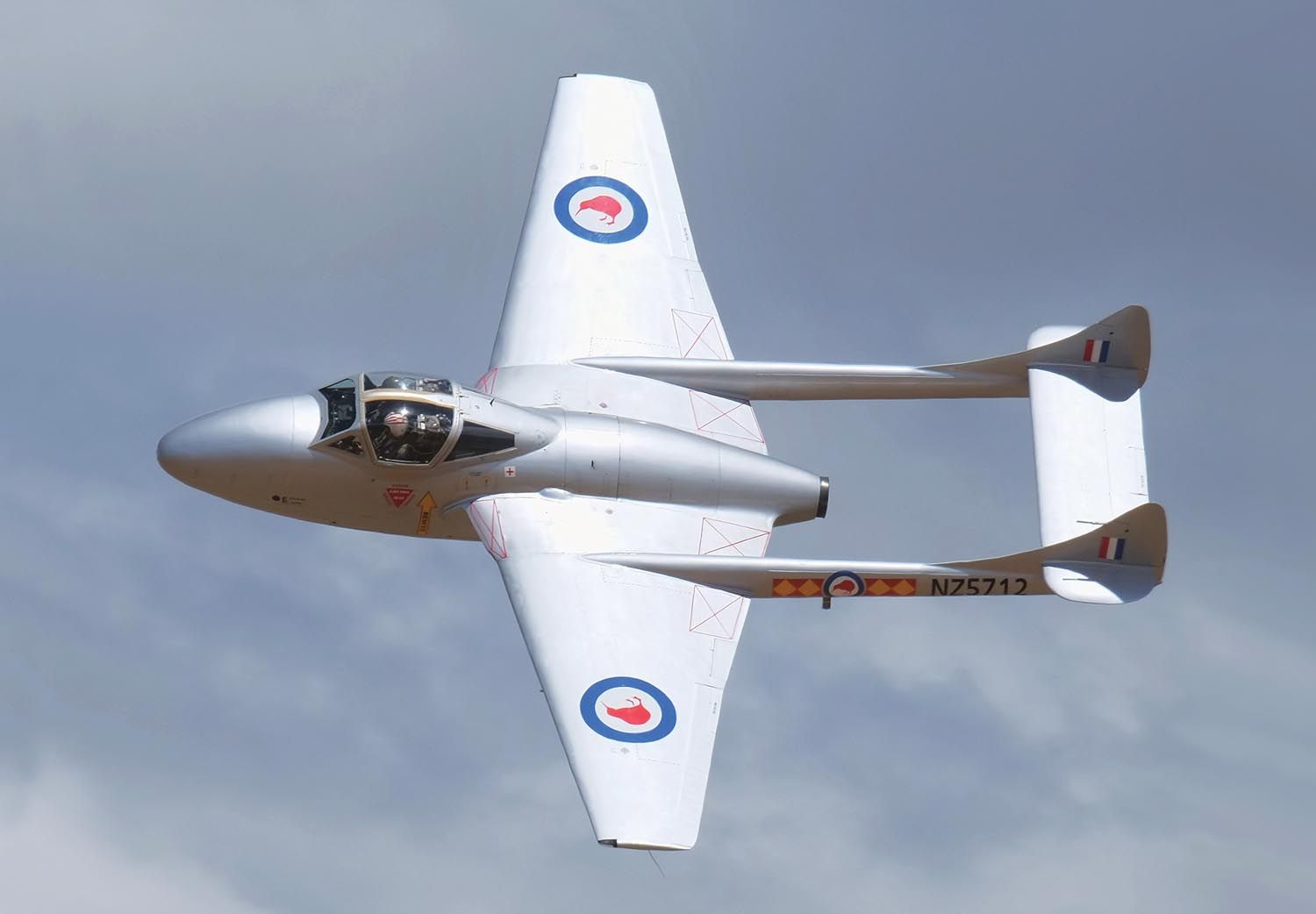
The task of an airplane designer is to generate a design for an airplane that flies successfully and executes the user’s mission. The manufacturer must be able to build the airplane and sell them in sufficient numbers to generate sufficient revenue to stay in business and make a profit.
The designer must consider all three factors: Mission, Manufacturing and Marketing.
We have already considered “mission” in some detail in previous editions of Wind Tunnel, so we now turn our attention to the other “M’s.”
Manufacturing
The first choice the designer must make is what materials the airplane will be made of and what manufacturing processes will be needed to fabricate the parts and assemble the airplane.
Usually there will be more than one set of materials that will meet the strength, durability and surface quality requirements for the airplane. The choice of materials will, in turn, determine the type of manufacturing technology, tooling and workforce skills needed to build the airplane.
Materials Cost and Availability
The cost and availability of materials is a primary design consideration. It’s much cheaper to make an airplane of readily available standard materials and to design the parts so they can be fabricated from standard stock. Sometimes, even the detailed choice of material can make a big difference. For example, many homebuilt and kit airplanes use 6061-T6 aluminum, which is a very commonly used alloy, instead of 2024 or 7075 alloys, which are typically aerospace-only. The aerospace alloys have higher yield strength than 6061-T6 but cost two to three times as much per pound. For the majority of light plane structures, the extra strength does not offset the higher cost of the aerospace alloys. The lower yield strength of the 6061-T6 is more than adequate for most lightly loaded areas like skins, and in more highly loaded areas, a somewhat thicker 6061-T6 part can safely replace a part made of 2024 or 7075 alloy.
Any part that requires specially sourced material will be very expensive. High-end military airplanes and large transport airplanes, for example, need specialized metal forgings for major structural components like main bulkheads and wing primary structure. These are prohibitively expensive for all but the most sophisticated and highly produced airplanes.
Skill Base
There is a wide variation of the skills required and the skills the designer can expect the fabricators of the airplane to have.
A homebuilder may start with very little skill and learn as they go. The designer of a kit airplane or one intended to be built from scratch by a single individual must take this into account. The skills needed to fabricate the airplane should be relatively easy to learn, and the design should have enough reserve and redundancy so that minor fabrication and assembly imperfections will not compromise the safety of the completed airplane.
Higher end and series production require more and more specialized skills.
Changing materials requires retraining both in engineering and fabrication. The skills needed to build a fabric-covered airplane with a wooden wing structure and steel-tube fuselage structure are different than the skills needed to build an all-metal airplane with sheet metal skins. High-end metal airplanes (fighters and transports) require specialized skills to fabricate the large machined parts like primary bulkheads and wing spars, as well as the many complex machined parts in the systems. Composites fabrication requires yet another skill set that is entirely different from metal fabrication.
This phenomenon affects the adoption of new materials and manufacturing processes.
It can also have some interesting effects on the availability and operational effectiveness of an airplane. One good example of this is the persistence of wood and fabric in WW-II airframes. At the time of the Battle of Britain the RAF was flying Hawker Hurricanes and Supermarine Spitfires to defend England. The Hurricane was already obsolescent: It had a steel-tube fuselage structure with wooden formers and stringers shaping its fabric covering. The Spitfire was of all-metal construction. The Hurricane’s “obsolete” structure meant that it could be built and rapidly repaired by a large number of British workers using simple, widely available tools, while production of the Spitfire required newly developed skills and complex, specialized tooling. As a result, the RAF initially had more Hurricanes than Spitfires and was able to keep them flying more easily. In fact, Hurricanes shot down more enemy airplanes than Spitfires during the Battle of Britain.
Times change, and in today’s world the skills needed to do the woodwork on a Hurricane are rare, while aircraft metalworking skills and tools are common. Because of this, while Hurricanes were easier and quicker to build originally, it now takes far more time and effort to restore a Hurricane than a Spitfire.
Wooden construction probably reached its apex with the DH Mosquito, which was specifically designed to take advantage of the availability of wood and woodworkers to augment aircraft production beyond what could be achieved with metal-only airframes at the time. De Havilland persisted with wood into the jet age. The fuselage of the Vampire jet fighter is made of wood in much the same way as that of the Mosquito.
Capital Plant and Cost of Tooling
Another important consideration for the designer is the nonrecurring expense (NRE) of setting up the manufacturing facility and the machinery and tooling needed to fabricate the parts of the airplane.
There is often a trade-off between the labor hours required to fabricate each part and the cost of the tooling used to make it. The best approach will depend on how many airplanes you plan to produce and how fast you plan to produce them. The more airplanes and the higher the production rate, the more value there is in investing in tooling to automate production and minimize touch labor.
The cost of tooling can also affect the configuration and design of the airplane. Design features that can only be made using expensive, specialized tools should only be adopted if they provide a worthwhile advantage over simpler-to-make alternatives.
For example, forming compound curves in metal requires stretch-forming, which is very labor-intensive if it is done by hand and requires expensive precision tooling to automate. This is why the majority of metal airplane skins are lofted to be flat-wrapped from sheet material.
Another example where tooling costs affect configuration is the common use of constant-chord metal wings on light airplanes. Fabricating metal ribs requires the metal to be shaped over a precisely shaped form block. Each rib shape requires its own specific form. All of the ribs for a constant-chord wing can be made using the same tooling, while each rib for a tapered wing requires its own unique tool.
An optimized tapered wing will be lighter and more aerodynamically efficient than a constant-chord wing, but often alleviating the performance penalty of the constant-chord wing does not justify the extra cost of tooling to make the tapered wing.
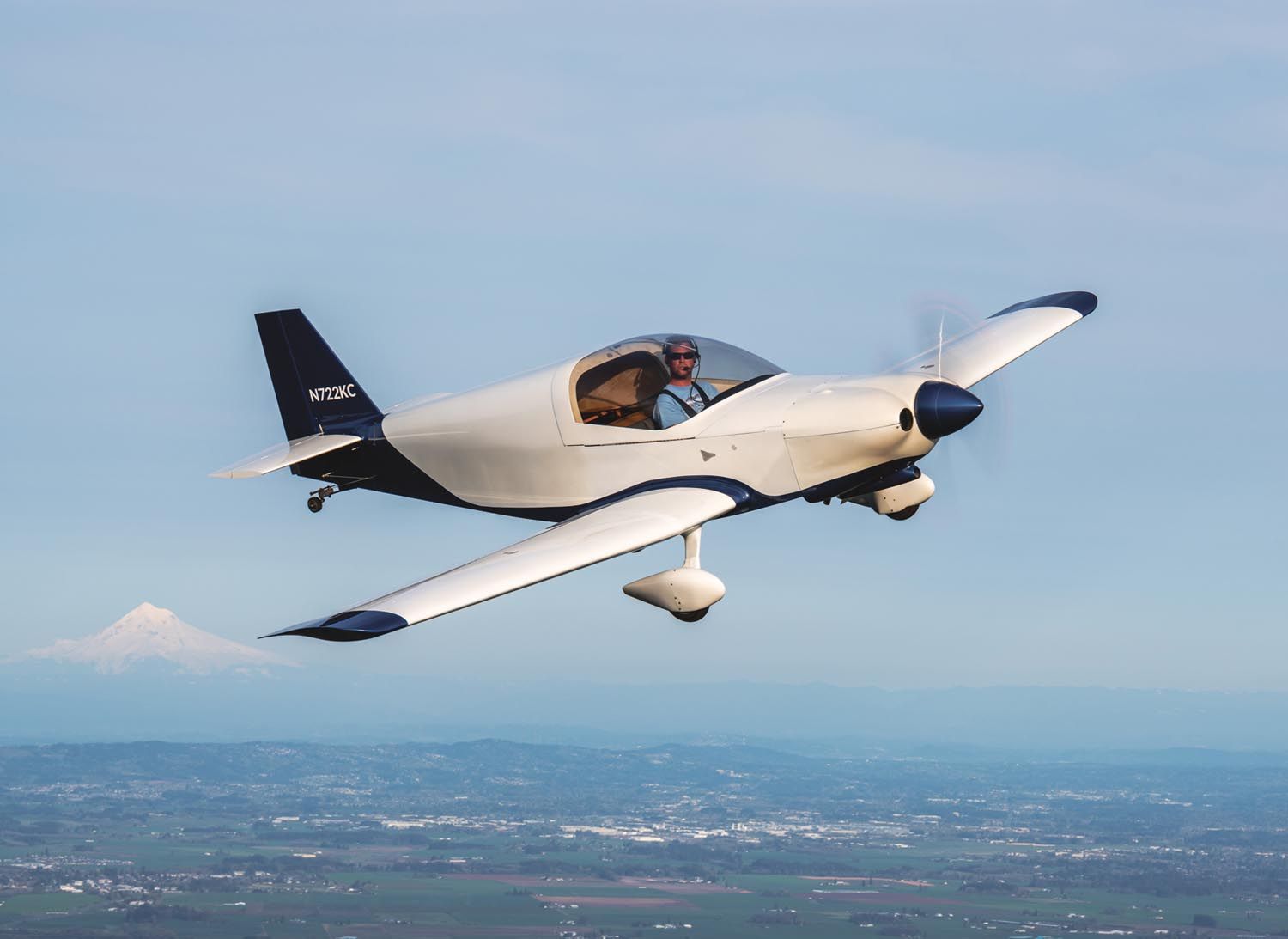
Manufacturing Technology
Changes in manufacturing technology periodically change how we build airplanes and open up new possibilities. Sometimes, they also rehabilitate an older approach by significantly changing the cost and/or skill required to make parts.
The adoption of composites by the homebuilt and kit airplane community was driven primarily by tooling and fabrication considerations. The improvements in aerodynamic performance and additional freedom to shape airplanes optimally was a side benefit.
Hand-fabricating traditional wood and steel-tube aircraft structures or sheet metal structures is time-intensive, particularly if one has to hand-form metal ribs and bulkheads.
Moldless composite construction, pioneered by Ken Rand on the KR-1 and Burt Rutan with the VariEze, made it much easier for a homebuilder to build an aerodynamically smooth wing relatively quickly with a minimum of tooling.
Molded composites made kits like the Glasair and Lancair, with a high degree of prefabrication at the factory, possible. Producing these kits required a set of molds for the large parts, but these were far less expensive than the tooling needed to fabricate metal airplane parts using traditional methods.
All-metal airplane parts took many hours to fabricate by hand and expensive tooling to manufacture. Flat metal parts required expensive punch dies to manufacture in quantity, and every unique part needed its own tool to make.
Computer-aided design (CAD) and numerically controlled (NC) machinery revolutionized metal airplane fabrication. Flat metal parts can be cut using a variety of NC cutting systems including water-jet, NC routers or laser cutting. The machinery that does the cutting is not configuration-specific to the parts. Standard industrial machines can be programmed to make the parts, and it’s not even necessary for the airplane manufacturer to own the machines because it’s relatively easy to contract with commercial metal-cutting shops to make parts.
More sophisticated NC machinery can make machined parts and fittings.
Very capable CAD software is now available that will run on most personal computers, so the overall cost of access to CAD and NC fabrication has dropped to the point where its available to the individual designer/builder.
This numerical manufacturing revolution fundamentally changed the kit market. In much the same way that composite kits replaced scratch-built metal or wood-and-steel-tube airplanes as the primary choice of homebuilders, the highly prefabricated metal kits that NC manufacturing made possible have overtaken composite kits in sales and completions.
Next month, we will take a look at the third “M”: Marketing. Many design choices are driven not by technical considerations, but by what will appeal to potential buyers.
Whatever happened to the Facetmobile?
Latest for Facetmobile FMX-7 BatRay see
https://barnabywainfan.substack.com/p/oshkosh-2024-forums-and-batray-progress
Latest for Facetmobile FMX-4 N292FM s/n 1002 see
https://www.eaa292.org/content.aspx?page_id=22&club_id=486834&module_id=650788
2022 dec page 7 and 14